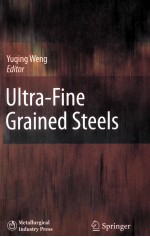
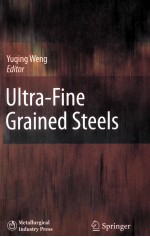
超细晶钢 英文版PDF电子书下载
- 电子书积分:17 积分如何计算积分?
- 作 者:翁宇庆等著
- 出 版 社:北京:冶金工业出版社
- 出版年份:2008
- ISBN:9787502444150
- 页数:569 页
1 Overview 1
1.1 The Technology of Controlled Rolling and Controlled Cooling 2
1.2 R&D Program of"Super Steels"and"New Generation Steel Materials" 7
1.3 The Formation of Ultra-fine Grains and Microstructural Refinement of Steels-Core Technique for the R&D of New Generation Steel Materials 10
1.4 Theory and Technology on Ultra-fine Grains 19
1.4.1 The state change and microstructure refinement of austenite during hot deformation 19
1.4.2 Deformation induced ferrite transformation 20
1.4.2.1 Thermodynamic consideration of deformation induced ferrite transformation 21
1.4.2.2 DIFT phase transformation and characters of transformed products 23
1.4.3 Deformation induced precipitation and medium temperature phase transformation control 26
1.4.4 The influence of nanometer size precipitates on ultra fine grain steel 31
1.4.5 Ultragrain refinement of alloy structural steels and the way of increasing the resistance against delayed fracturing 35
1.4.6 The development of carbide-free bainite/martensite multiple phase steels 38
1.5 Several Key Technologies Concerning the Development of Ultra Fine Grain Steels 41
1.5.1 Steel cleanness 42
1.5.2 Refinement and homogenization of solidification structure 45
1.5.3 Brief introduction of welding technique and economy of ultra fine grain steels 47
References 51
2 Refinement of Austenitic Microstructure and Its Influence on γ→α Transformation 53
2.1 Thermomechanical Control Process and Refinement of Austenitic Microstructure 53
2.1.1 Rolling at the austenite-recrystallization temperature region(RARTR) 56
2.1.1.1 Metadynamic recrystallization 63
2.1.1.2 Static recrystallization 65
2.1.2 Rolling in austenite non-recrystallization temperature region 70
2.1.3 Rolling at the under-cooled austenite 73
2.1.4 Accelerated cooling and microstructural refinement 78
2.2 Influence of Austenitic Recrystallization on Subsequently Transformed Grain Size 79
2.2.1 Influence of recrystallized or deformed austenite on ferrite transformation 79
2.2.1.1 Influence of recrystallized austenite on ferrite transformation 79
2.2.1.2 Influence of partially recrystallized austenite on ferrite transformation 80
2.2.1.3 Influence of non-recrystallized austenite on ferrite transformation 80
2.2.2 Influence ofrecrystallization in the austenite on DIFT 81
References 82
3 Deformation Induced Ferrite Transformartion 86
3.1 Introduction 86
3.2 Experimental Confirmation and Study Method of DIFT 88
3.2.1 Microstructure observation on the quenched sample 88
3.2.2 Mechanical behavior measurement 89
3.2.3 Dilatometry measurement 90
3.2.4 In-situ X-ray diffraction 92
3.3 Thermodynamics of DIFT 93
3.3.1 Deformation stored energy 93
3.3.2 Transformation driving force 95
3.3.3 Ad3 versus deformation stored energy 96
3.4 Kinetics of DIFT 98
3.4.1 Microstructural evolution and nucleation sites 99
3.4.2 Transformation fraction versus strain 102
3.4.3 Ferrite grain number and grain size versus transformation fraction 104
3.4.4 Theoretical analysis 105
3.4.4.1 Ferrite nucleation rate and deformation stored energy 105
3.4.4.2 Ferrite grain growth and deformation stored energy 106
3.5 Mechanisms of DIFT 108
3.6 Factors Influencing DIFT 109
3.6.1 Deformation variables 110
3.6.1.1 Strain 110
3.6.1.2 Deformafion temperature 110
3.6.1.3 Strain rate 114
3.6.2 Chemicai compositions 115
3.6.2.1 Effect of carbon and manganese 115
3.6.2.2 Effect of niobium and vanadium 117
3.6.3 Prior austenite grain size 127
3.7 Applications of DIFT 127
3.7.1 Applications of DIFT in plain low carbon steel 127
3.7.1.1 Plain low carbon steel rebar 128
3.7.1.2 Plain low carbon steel strip 129
3.7.2 Applications of DIFT in microalloyed steel 131
3.7.2.1 Laboratory trial production of 700MPa grade ultrafine grained steel 131
3.7.2.2 Industrial production of high strength Cu-P-Cr-Ni weathering resistance steel 132
References 134
4 Microstructure Refinement of Steels by TSCR Technology 137
4.1 Microstructure Refinement Process and Austenite Recrystallization of Low Carbon Steels Produced by TSCR Technology 137
4.1.1 Contrast between TSCR technology and traditional technology 137
4.1.2 The refinement process of microstructure during CSP hot continuous rolling 140
4.1.2.1 Variation of the grain size in rolling direction 141
4.1.2.2 Variation of grain size in rolling plane 142
4.1.2.3 Comparison of microstructure in transverse,rolling and surface direction of ZJ330 rolling block workpiece for different passes 143
4.1.3 The relationship between texture and the austenite and the ferrite 144
4.1.3.1 Texture analysis by EBSD 144
4.1.3.2 Orientation analysis by EBSD 146
4.1.4 Austenite recrystallization of low carbon steel during continuous hot rolling process 147
4.1.4.1 Microstructure evolution model of austenite during hot continuous rolling for low carbon steel 148
4.1.4.2 Simulation of microstructure evolution for austenite during hot continuous rolling of low carbon steel 150
4.2 Microstructure and Properties of Low Carbon Steel Produced by Thin Slab Casting and Rolling(TSCR) 153
4.2.1 Comparison on microstructure and properties of low carbon hot strip with different thermal histories 153
4.2.1.1 Production comparison experiments of CSP and traditional technology in producing hot low carbon strip 153
4.2.1.2 Comparison and analysis of mechanical properties and microstructure of strips produced by two kinds of process 154
4.2.2 Analysis of structure property in low carbon hot strip produced by CSP and traditional process 156
4.2.2.1 Comparison of structure and property of low carbon hot strip produced by CSP and traditional process 156
4.2.2.2 Analysis of influencing factor on microstructure and properties of hot strip produced by CSP 159
4.2.2.3 Microstructure and properties of C-Mn strips with high strength produced by CSP process 160
4.3 Mechanism and Precipitation Characteristic of AlN in Low Carbon Steel Produced by Thin Slab Casting and Rolling Technology 164
4.3.1 AlN precipitation in low carbon steel of thin slab casting and rolling 164
4.3.1.1 Experirnent on precipitation of AlN during heating and rolling 164
4.3.1.2 Experiment analysis on precipitation of AlN in hot rolled strip by thin slab casting and rolling 165
4.3.2 Precipitation dynamics of AlN 166
4.3.2.1 Dynamics model of AlN precipitation 167
4.3.2.2 Dynamics condition of AlN and simulation result 170
4.3.3 Effect of fine AlN particles on structure and performance 173
4.3.3.1 Effect of AlN particles on the precipitation of austenite section 173
4.3.3.2 Effect of AlN precipitation during the phase transformation 174
4.4 Control on Soft Mechanism of Cold Rolling Thin Slab by Continuous Casting and Rolling 175
4.4.1 Requirements of cold-rolled sheet for deep drawing to the property of cold rolling billet and the control methods on soften steel 175
4.4.2 Mechanism of adding B micro-alloy into low-carbon steel on grain growth coursing and steel softening 176
4.4.2.1 Action of adding B micro-alloy into steel on the coursing of grain growth 176
4.4.2.2 Effects of adding B into steel on the precipitation in low carbon steel 177
4.4.3 Effects of the hot rolling and cooling technology on the softening of low carbon steel 181
4.4.3.1 The effects of finishing temperature on theperformance of SPHC 181
4.4.3.2 The effects of finishing reduction on the property of SPHC 181
4.4.3.3 The effects of coiling temperature on the property of SPHC 182
4.4.3.4 The effects of hot rolled lubrication on the property of SPHC 182
4.4.3.5 The effects of cooling methods on the property of SPHC 182
4.4.4 The effects of the control method of different softening technology on the formability of cold-rolled sheet 08Al 183
4.4.4.1 The composition and technology of hot rolled low carbon steel of CSP 184
4.4.4.2 The technologies of cold rolling and annealing 184
4.4.4.3 The effects of coiling temperature and total cold-rolled reduction on r-value of steel 08Al with and without B 185
4.4.4.4 The effects of coiling temperature and total cold-rolled reduction on the yield strength of08Al steel with and without B 186
4.4.4.5 The effects of coiling temperature and the total cold-rolled reduction on elongation percentage 188
4.4.4.6 Texture analysis of B free and B added steel 188
4.5 Precipitations in the CSP Low Carbon Steels 190
4.5.1 Introduction 190
4.5.2 Sulfide and oxide dispersive precipitates 191
4.5.2.1 Precipitates in slabs and rolling pieces of the low carbon steels 192
4.5.2.2 Sulfides in the low carbon steels with varying content of sulfur 198
4.5.2.3 Mechanism of the sulfide precipitation in the condition of CSP process 202
4.5.2.4 Effects of the sulfide and oxide on formation of other phases 214
4.5.2.5 Other nanometer precipitates in the steels 218
4.5.3 Carbides and carbonitrides in Ti containing steels 221
4.5.3.1 In general feature 221
4.5.3.2 Experimental investigation 223
Summary 227
References 228
5 Microstructure Fining Theory of Low-carbon Bainitic Steel 235
5.1 Social Needs for Low-carbon Bainitic Steel with a Grade of More than 600MPa 235
5.2 Strengthening Mechanism of Low(Ultra-low)Bainitic Steel 237
5.3 Primary Characteristics of Several Kinds of Low-carbon Bainitic Steels Developed in China 238
5.3.1 CCT curve characteristics of the steels 238
5.3.2 Recrystallization curve characteristics during hot-processing 240
5.3.2.1 C-Mn steel and Nb or B individually added steel 240
5.3.2.2 When alloying elements such as Nb,,B,Cu are combinedly added 241
5.3.3 PTT curve characteristics of the steel 242
5.4 Theoretical Thought for Furthering Fining the Intermediate-temperature Transformation Microstructures 246
5.4.1 Basic key points for intermediate temperature transformation microstructure fining 248
5.4.2 Theoretical background for proposing the relaxation-precipitation-controlling transformation(RPC)technology 249
5.4.3 Basic ideas of TMCP+RPC technology 251
5.5 Ultra-fining Process,Actual Fining Effect and Typical Microstructures 254
5.5.1 Selecting composition range of micro-alloying elements fully performing ultra-fining process effect 254
5.5.1.1 Principle of composition design 254
5.5.1.2 Starting points of composition selection 255
5.5.1.3 Strength evaluation 255
5.5.2 Typical process of relaxation-precipitation-controlling transformation(RPC)technology 257
5.5.3 Typical fining microstructures under RPC process and its comparison with other processes 258
5.5.4 Effects of RPC process and composition on microstructure and properties 263
5.5.4.1 Effect of relaxing time 264
5.5.4.2 Effects of final-rolling temperature 265
5.5.4.3 Effects of cooling rate on microstructure and properties 266
5.5.5 Strength,plasticity and toughness of the steel from industrial Trial Production of RPC process 267
5.6 Study on Fining Process Parameters of Intermediate-temperature Transformed Microstructure Through Thermo-mechanical Simulation 269
5.6.1 Microstructure evolution after deformation and relaxation under different temperatures 270
5.6.2 Quantitative statistics of bainitebundle size 273
5.7 Forming Mechanism of Typical Fining Microstructures 276
5.7.1 Two kinds of typical microstructure morphology in samples after RPC process 276
5.7.2 Formation and influence of substructure during relaxation 278
5.7.3 Induced precipitation in deformed austenite and Its effects(Yuan et al,2004;Yuan et al,2003) 280
5.7.4 Formation,Morphology of acicular ferrite and its effect on fining 288
5.7.4.1 Morphology characteristics of acicular ferrite 288
5.7.4.2 Effect of relaxation on formation of acicular ferrite 289
5.8 Study on the Variation of Microstructure and Properties of Fined Steels during Tempering and Its Cause Analysis 291
5.8.1 Hardness changes and their difference between the microstructure-fined steel and the quenched and tempered steel with the same compositions 291
5.8.2 Microstructure stability in tempering process 293
5.8.3 Effect of tempering temperature on mechanical properties of the steel 296
5.9 Concluding Note 297
References 298
6 Microstructure Refining and Strengthening of Martensitic Steel 300
Introduction 300
6.1 Challenges of High Strength Martensitic Steel 301
6.1.1 Delayed fracture 301
6.1.2 Fatigue failure 304
6.2 Microstructure Refinement in Toughening and Improving DF Property of Martensitic Steels 305
6.2.1 Technologies for martensitic microstructure refining 305
6.2.2 Effect of microstructure refinement on strength and toughness 306
6.2.3 Effect of microstructure refinement on DF resistance 310
6.2.3.1 Stress corrosion cracking 310
6.2.3.2 Sustained load tensile delayed fracture 312
6.2.3.3 Discussion of the dependence of DF resistance on grain size 315
6.3 Grain Boundary Strengthening in Improving DF Property of Martensitic Steels 318
6.3.1 Reducing segregation of impurities at grain boundaries 319
6.3.2 Controlling grain boundary carbide 321
6.3.2.1 Increasing tempering temperature 321
6.3.2.2 Intercritical quenching 322
6.3.2.3 Ausforming process 324
6.3.3 Effect of Mo alloying 325
6.3.3.1 Mo raising tempering temperature 326
6.3.3.2 Mo carbide as hydrogen trap 328
6.3.3.3 Mo controlling impurities and strengthening grain boundaries 329
6.3.3.4 Influence of Mo content 330
6.4 Controlling of Hydrogen Trap in Martensitic Steels to Improve Its DF Resistance 331
6.5 Effect of Cleanliness on the Fatigue Performance of High Strength Martensitic Steels 335
6.6 New Developed High Strength Martensitic Steels and Their Industrial Application 341
References 345
7 Carbide-free Bainite/Martensite(CFB/M) Duplex Phase Steel 350
7.1 CFB/M Duplex Phase Structure 351
7.2 Alloy Design of CFB/M Duplex Phase Steel by Tsinghua University Bainitic Steel R&D Center 352
7.2.1 Alloy design of CFB/M duplex phase steel and its structure 352
7.2.2 Effect of cooling rate on CFB/M duplex phase microstructure 356
7.2.3 Effect of CFB/M duplex phase microstructure on strength and toughness of the steel 357
7.3 Effect of Tempering on Strength and Toughness of CFB/M Duplex Phase Steel 359
7.3.1 Effect of CFB/M duplex phase microstructure on the initial temperature of temper embrittleness the first kind 361
7.3.2 Effect of CFB/M duplex phase microstructure on yield-tensile ratio of steel 367
7.4 Susceptibility to Hydrogen Embrittlement for CFB/M Duplex Phase High Strength Steel 369
7.4.1 Effect of hydrogen content on susceptibility to hydrogen embrittlement for CFB/M duplex phase high strength steel 370
7.4.2 Effect of heat treatment process on susceptibility to hydrogen embrittlement for CFB/M duplex phase high strength steel 374
7.4.2.1 Effect of BU and CFB 376
7.4.2.2 Effect of CFB quantity on fracture surface topography 378
7.4.3 Influence of microstructure refinement and retained austenite on susceptibility to hydrogen embrittlement for CFB/M steel 379
7.5 Stress Corrosion of CFB/M Duplex Phase High Strength Steel 385
7.5.1 Stress corrosion cracking property of CFB/M duplex phase high strength steel 385
7.5.2 Stress corrosion fracture of CFB/M duplex phase high strength steel 388
7.6 Hydrogen in CFB/M Duplex Phase High Strength Steel 391
7.6.1 Measure hydrogen diffusion coefficient using double electrolysis cell 392
7.6.2 Hydrogen trap in CFB/M duplex phase high strength steel 396
7.6.2.1 Bainitic/martensite lath boundary 398
7.6.2.2 Retained austenite 398
7.7 Mechanism of Resistance to Delayed Fracture of CFB/M Steel 402
7.7.1 Relationship between susceptibility to hydrogen embrittlement and hydrogen trap for CFB/M steel 402
7.7.2 Relationship between stress corrosion and hydrogen trap in steel 403
7.7.3 Crack propagation model of CFB/M duplex phase steel 405
7.8 Fatigue Behavior of 1500MPa CFB/M Duplex Phase High Strength Steel 405
7.8.1 Fatigue behavior of CFB/M duplex phase steel 405
7.8.1.1 Fatigue strength of CFB/M duplex phase steel 405
7.8.1.2 Fatigue crack propagation behavior 406
7.8.1.3 Fatigue fracture of CFB/M duplex phase high strength steel 410
7.8.2 Effect of microstructure characteristics of CFB/M duplex phase steel on fatigue behaviors 413
7.8.2.1 Effect of microstructure characteristics on fatigue strength 413
7.8.2.2 Effect of microstructure characteristics on △Kth and da/dN 416
7.8.3 Effect of retained austenite on fatigue behaviors of CFB/M duplex phase steel 419
7.8.3.1 Retained austenite content and cyclical stability 419
7.8.3.2 Effect of retained austenite and its cyclical stability on fatigue strength 420
7.8.3.3 Effect of retained austenite film on fatigue crack propagation 421
7.8.4 Fatigue fracture mechanism of CFB/M duplex phase steel 422
7.9 Application Prospect of CFB/M Duplex Phase Steel 422
References 424
8 Extra Low Sulfur and Non-metallic Inclusions Control for Ultra Fine Grain High Strength Steels 431
8.1 Introduction 431
8.2 Refining Technology for Extra Low Sulfur Steels 432
8.2.1 Hot metal De-S pretreatment 433
8.2.2 Reducing[S]pick up in BOF steelmaking 435
8.2.3 Desulfurization in secondary refining of liquid steel 438
8.2.3.1 Desulfurization during BOF tapping 441
8.2.3.2 Desulfurization in ladle furnace refining(LF) 443
8.2.3.3 Powder injection desulfurization methods 444
8.3 Extra Low Oxygen and Non-metallic Inclusions Control of High Strength Alloying Steels 447
8.3.1 Influence of non-metallic inclusions on fatigue property of steel 448
8.3.2 Refining and non-metallic inclusion control of extra low oxygen alloy steels 450
8.3.3 Deformable non-metallic inclusions for tyre cord and valve spring steels 458
8.3.3.1 Deformable non-metallic inclusions 459
8.3.3.2 Control of[Al]in liquid steel 461
8.3.3.3 Slag control 462
8.3.4 Steel with premium cleanliness 468
References 470
9 Fundamental Study on Homogeneity of Solidification Structure of Steel 473
9.1 The Structure of Liquid Fe-C Alloy 473
9.1.1 Experimental 473
9.1.2 Data analysis 474
9.1.3 Medium-range order structure in liquid Fe-C alloy 475
9.1.4 Conclusions 479
9.2 Observation and Analysis of Heterogeneous Nucleation Phenomena 480
9.2.1 Experimental 481
9.2.2 Effects of vibration frequency and amplitude 482
9.2.3 Effects ofsolid substrate temperature and surface roughness 483
9.2.4 Conclusions 486
9.3 Homogeneity and Equiaxed Grain Structure of Steels 486
9.3.1 Relation of segregation and equiaxed grain structure 487
9.3.2 Titanium-based inoculation technology 488
9.3.2.1 Precipitation of TiN particles 488
9.3.2.2 Competitive precipitation between TiN and Ti2O3 489
9.3.2.3 Particles for nucleus ofδ-ferrite dendrites 490
9.3.3 Small temperature gradient technology 491
9.3.4 Conclusions 492
References 492
10 Welding of Ultra-Fine Grained Steels 494
10.1 Introduction 494
10.2 Simulation of Welding of Fine-grained Steel 495
10.2.1 Simulation of grain growth in HAZ 495
10.2.1.1 The monte carlo model of the HAZ 496
10.2.1.2 The EDB model 497
10.2.1.3 MC simulation ofgrain growth in HAZ of fine-grained steels 498
10.2.1.4 Experimental identification 499
10.2.2 Fluid flow in welding pool of ultra fine grain steel 501
10.2.2.1 Mathematical model 501
10.2.2.2 Numerical method 505
10.3 Welding of Fine Grained Carbon Steel Plate 509
10.3.1 Laser welding of low carbon steel 509
10.3.1.1 Experiment material and equipment 509
10.3.1.2 Weld shape and microstructure of welded joints 510
10.3.1.3 Mechanical properties of laser welded joint 514
10.3.1.4 Conclusions 517
10.3.2 Arc welding of fine grained low carbon steel 518
10.3.2.1 Experiment material and method 518
10.3.2.2 Experiment results and discussion 519
10.3.2.3 Conclusions 523
10.3.3 Arc welding of fine grained atmospheric corrosion resistant steel 524
10.3.3.1 Experiment materials and procedure 524
10.3.3.2 Experiment results and discussion 525
10.3.3.3 Conclusions 527
10.3.4 Welding of 400 MPa grade fine grained rebar 528
10.3.4.1 Experiment material and procedure 528
10.3.4.2 Experiment results and discussion 529
10.3.4.3 Conclusions 531
10.4 Welding of Ultra-Fine Structure Bainite Steel 532
10.4.1 Development of ultra-low carbon bainitic high strength welding wire 532
10.4.1.1 Designing principles of the ULCB welding wires 532
10.4.1.2 Compositions and mechanical properties of ULCB wire deposited metals 533
10.4.1.3 Optical microstructure of the ULCB deposited metals 536
10.4.1.4 Fine microstructure of ULCB wire deposited metals 538
10.4.1.5 Conclusions 539
10.4.2 Microstructures and properties of the GMAW welded joint of the ultra fine structure bainitic steel 540
10.4.2.1 Weld microstructure of ultra fine grained bainitic steel 540
10.4.2.2 Mechanical properties of weld metal in ultra-fine grained bainitic steel 543
10.4.2.3 Conclusions 545
10.4.3 Laser welding of ultra-fine microstructural bainitic steel 546
10.4.3.1 Chemical composition and microstructure of base metal 546
10.4.3.2 Experimental procedure 547
10.4.3.3 Grain size 548
10.4.3.4 Microstructure of CGHAZ 549
10.4.3.5 Hardness and strength of CGHAZ 553
10.4.3.6 Toughness of CGHAZ 555
10.4.3.7 Conclusions 560
References 561
Subject Index 567
- 《卓有成效的管理者 中英文双语版》(美)彼得·德鲁克许是祥译;那国毅审校 2019
- 《AutoCAD 2018自学视频教程 标准版 中文版》CAD/CAM/CAE技术联盟 2019
- 《跟孩子一起看图学英文》张紫颖著 2019
- 《AutoCAD机械设计实例精解 2019中文版》北京兆迪科技有限公司编著 2019
- 《复分析 英文版》(中国)李娜,马立新 2019
- 《张世祥小提琴启蒙教程 中英文双语版》张世祥编著 2017
- 《生物化学 本科临床 英文版》张晓伟 2018
- 《理想国 全英文原版》(古希腊)柏拉图著 2017
- 《Dreamweaver CC 2018标准实例教程 中文版》杨雪静,胡仁喜编著 2019
- 《Flash CC动画制作实用教程 中文版》麓山文化 2019
- 《指向核心素养 北京十一学校名师教学设计 英语 七年级 上 配人教版》周志英总主编 2019
- 《北京生态环境保护》《北京环境保护丛书》编委会编著 2018
- 《指向核心素养 北京十一学校名师教学设计 英语 九年级 上 配人教版》周志英总主编 2019
- 《高等院校旅游专业系列教材 旅游企业岗位培训系列教材 新编北京导游英语》杨昆,鄢莉,谭明华 2019
- 《中国十大出版家》王震,贺越明著 1991
- 《近代民营出版机构的英语函授教育 以“商务、中华、开明”函授学校为个案 1915年-1946年版》丁伟 2017
- 《新工业时代 世界级工业家张毓强和他的“新石头记”》秦朔 2019
- 《智能制造高技能人才培养规划丛书 ABB工业机器人虚拟仿真教程》(中国)工控帮教研组 2019
- 《陶瓷工业节能减排技术丛书 陶瓷工业节能减排与污染综合治理》罗民华著 2017
- 《全国职业院校工业机器人技术专业规划教材 工业机器人现场编程》(中国)项万明 2019