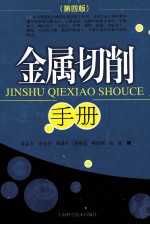
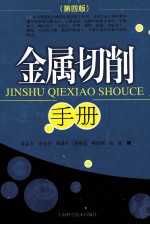
金属切削手册PDF电子书下载
- 电子书积分:29 积分如何计算积分?
- 作 者:诸全兴,侯慧人等编
- 出 版 社:上海:上海科学技术出版社
- 出版年份:2011
- ISBN:9787547805527
- 页数:1153 页
第一章 金属切削基本知识 1
一、一般名称及术语 1
1.工件上的表面 1
2.刀具的组成要素 1
3.切削运动 3
二、刀具的几何角度 4
1.确定刀具几何角度的参考系 4
(1)静态参考系 4
(2)工作参考系 6
2.刀具几何角度的定义 7
(1)刀具的静态几何角度 7
(2)刀具的工作几何角度 8
3.单刃刀具的几何角度标注方法 10
(1)按Po-Pr-Ps正交平面系标注 11
(2)按Pn-Pr-Ps法平面系标注 11
4.刀具几何角度的换算 11
(1)同一参考系内的角度换算关系 11
(2)刀具的静态角度与工作角度的关系 13
5.刀具几何参数的选择 15
(1)刀具几何角度的作用及选择原则 15
(2)刀尖形状及其参数的选择 17
(3)切削刃形式及其参数的选择 17
三、切削用量、切削层及材料切除率 19
1.切削用量三要素及其选择原则 19
(1)切削速度 19
(2)进给量 19
(3)背吃刀量 19
2.切削层的参数 21
(1)切削层公称厚度 21
(2)切削层公称宽度 21
(3)切削层公称横截面积 21
3.材料切除率 22
四、刀具切削部分材料 22
1.各类刀具材料的基本性能 22
2.高速钢的分类、钢号、性能及用途 24
3.硬质合金 26
(1)切削加工用硬质合金的分类、分组代号 26
(2)常用硬质合金的分类、化学成分、力学性能 28
(3)国内主要厂商生产的硬质合金牌号及其适用范围 29
(4)涂层硬质合金 33
(5)硬质合金刀片的型号规格 35
4.陶瓷刀具材料 42
5.超硬刀具材料 43
五、切削过程的基本概念 46
1.切屑的形成过程及切削力和切削热 46
2.积屑瘤 47
3.切削力及切削功率的估算 49
(1)单位切削功率 49
(2)计算实例 50
4.刀具的磨损及破损 51
(1)刀具磨损的形式 51
(2)刀具磨损的原因 52
(3)刀具的磨损限度 53
(4)刀具寿命 54
(5)解决硬质合金刀具崩刃打刀的措施 55
六、已加工表面质量 57
1.衡量表面质量的指标 57
2.表面粗糙度 57
(1)各种加工方法所能达到的表面粗糙度 57
(2)减小表面粗糙度的措施 59
3.加工硬化及残留应力 60
(1)形成加工硬化及残留应力的原因 60
(2)加工钢材时工件表面的硬化情况 61
(3)减小加工硬化及残留应力的措施 61
七、切削液 62
1.切削液的作用 62
2.切削液的种类 63
(1)各种切削液的性能特点 63
(2)常用切削液的性能及适用范围 64
3.切削液的使用方法 66
4.减少切削液对环境影响的措施 68
八、切屑的控制 69
1.切屑形状的分类 69
2.切屑控制的基本要求 70
3.断屑方法及影响断屑的因素 70
4.断屑槽的设计 72
(1)断屑槽槽形及其参数的选择原则 72
(2)中等切深下切削低碳钢或中碳钢的断屑槽参数 73
(3)中等切深下切削合金结构钢或工具钢的断屑槽参数 73
(4)大切深下切削碳素钢或合金结构钢的断屑槽参数 73
(5)小切深下切削钢件的断屑槽参数 74
(6)小月牙洼断屑槽槽形参数及断屑范围 74
九、工件材料的切削加工性 75
1.工件材料切削加工性的分级、影响因素及改善途径 75
(1)切削加工性的分级 75
(2)影响切削加工性的因素 76
(3)改善工件材料切削加工性的途径 77
2.不锈钢的切削加工 77
(1)不锈钢的分类 77
(2)各类不锈钢的相对加工性系数 78
(3)不锈钢难切削的原因 78
(4)切削不锈钢的具体措施 79
3.高温合金的切削加工 79
(1)高温合金的分类 79
(2)高温合金难切削的原因 80
(3)切削高温合金的具体措施 80
4.钛合金的切削加工 81
(1)钛合金的分类 81
(2)钛合金难切削的原因 81
(3)切削钛合金的具体措施 82
5.其他难切削材料的加削加工 82
(1)高硬度材料的切削加工 82
(2)高锰钢的切削加工 83
十、可转位刀具的简介 84
1.可转位刀具的特点 84
2.硬质合金可转位刀片的选择 84
(1)可转位车刀刀片的形状及断屑槽选择 84
(2)可转位铣刀刀片的选择 86
3.刀片的夹持结构 86
(1)对刀片夹持结构的要求 86
(2)车刀刀片的夹持 86
(3)铣刀刀片的夹持 92
第二章 车削加工 97
一、不同形面加工工艺方案 97
1.外圆加工工艺方案比较 97
2.孔加工工艺方案比较 97
3.平面加工工艺方案比较 98
(1)粗加工 98
(2)精加工 99
(3)光整加工 99
二、机械加工中的定位与夹紧符号 99
1.基本符号 99
2.常用符号 100
3.实例说明 101
三、轴、套类零件的结构要素 101
1.中心孔的型式和尺寸 101
(1)不带护锥的A型中心孔 101
(2)带护锥的B型中心孔 102
(3)带护锥及螺孔的C型中心孔 102
(4) R形圆弧形中心孔 103
2.轴与套的倒角、倒圆角半径 104
3.端面及内、外圆的砂轮越程槽 104
四、轴、套类零件的磨削加工余量 105
1.外圆的磨削加工余量 105
2.内圆的磨削加工余量 105
五、车刀的选用 106
1.概述 106
2.外圆车刀几何参数的选择 106
(1)选择车刀几何参数的参考因素 106
(2)外圆车刀几何参数的参考数值 107
六、车削外圆 109
1.不同精度外圆的车削加工方法和加工余量 109
2.常用外圆车刀介绍 109
3.车削外圆时工件常用的装夹方法 114
4.中心架、跟刀架的应用及细长轴加工特点 116
(1)中心架的使用 116
(2)跟刀架的使用 117
(3)跟刀架的改进 118
(4)细长轴的加工特点 118
5.车削外圆产生故障和缺陷的原因及预防措施 121
七、车削圆柱孔 123
1.车床常用孔加工刀具及典型的加工方法 123
(1)车床上钻孔的方法 123
(2)常用镗孔刀的种类 125
(3)加工小孔内槽刀具及加工方法 126
2.车床镗孔微量调节切深方法 127
3.圆柱孔的测量方法 128
(1)用内卡钳测量圆柱孔 128
(2)用极限塞规测量圆柱孔 129
(3)用自制量棒测量大孔 129
(4)用游标卡尺测量圆柱孔 129
(5)用内径百分尺测量圆柱孔 129
(6)用内径百分表测量圆柱孔 130
4.车床上加工圆柱孔产生缺陷的原因及预防措施 131
八、切断与切槽 132
1.切断的特点 132
2.常用切断刀的几何参数 133
3.常用切断刀的主切削刃形状 134
4.硬质合金切断刀的切削用量 135
5.反切刀切断法 135
6.外沟槽的车削 136
(1)直槽的车削方法 136
(2)45°外沟槽车刀和车削方法 136
7.在车床上加工∞字形油槽 136
8.切断存在的常见问题 137
九、车削圆锥面 138
1.圆锥体各部分名称及计算 138
2.常用标准锥度及应用范围 139
3.标准圆锥 141
(1)莫氏圆锥 141
(2)公制圆锥 141
4.铣床主轴用刀杆尾部7:24圆锥 143
5.ST型手动换刀机床用7:24圆锥工具柄部 143
6.锥度和角度公差 144
7.自由角度和自由锥度公差 144
8.长圆锥面的车削方法 145
(1)机床附设机构的原理 145
(2)滚筒直径计算 145
9.车削小工件圆锥面的靠模装置 146
10.圆锥的检验方法 147
(1)单项测量法 147
(2)综合测量法 148
11.车削圆锥时产生缺陷的原因及预防方法 149
十、车削偏心工件 149
1.偏心工件的划线步骤 150
2.偏心工件常用的车削方法 150
3.偏心工件的测量方法 152
十一、车削特形面 153
1.用成形车刀车削特形面 153
2.用靠模车削特形面 154
3.车削内、外球面的几种刀具和方法 156
4.旋风切削球面的方法 156
5.特形面零件的检验方法 157
6.车削特形面产生缺陷的原因及预防方法 157
(1)车削后工件轮廓不正确 157
(2)特形面工件表面粗糙度不合格 158
十二、表面修饰加工 158
1.表面滚花加工 158
(1)滚花刀 158
(2)滚花方法 158
(3)花纹种类的选择和应用 158
2.表面滚压加工 158
(1)滚压加工原理 158
(2)滚压加工特点 158
(3)不同滚压加工的效果 161
(4)外圆滚压加工工具 161
(5)可调式浮动内圆滚压工具 162
(6)深孔滚压工具 164
(7)圆柱孔脉冲滚压工具 165
十三、典型零件加工工艺分析 168
1.生产过程 168
2.生产纲领、批量和生产类型 168
3.工艺过程 168
4.拟定工艺过程的注意事项 170
(1)工序的集中与分散 170
(2)划分加工阶段 170
(3)合理安排热处理工序 171
5.不同类型零件加工工艺分析 172
(1)概述 172
(2)轴类零件的加工实例分析 172
十四、特殊型面加工工艺分析 181
1.内双曲面车削工艺方法 181
(1)双曲面形成原理 181
(2)转角α的计算 182
(3)注意事项 182
2.多边形零件车削工艺方法 183
(1)概述 183
(2)专用装置的结构 183
(3)刀具及有关问题 183
(4)加工非正多边形工件的有关问题 186
3.钻削小直径深孔装置及刀具 187
十五、超硬材料刀具 188
1.超硬材料聚晶复合片 188
2.超硬材料车刀的几何参数 189
(1)聚晶金刚石车刀 189
(2)立方氮化硼车刀 190
3.超硬刀具的应用实例 190
(1)聚晶金刚石(PCD)刀具 190
(2)聚晶立方氮化硼(PCBN)车刀 194
第三章 螺纹加工 199
一、常用螺纹的种类、特征及其用途 199
二、螺纹的结构要素 207
1.普通外螺纹收尾、肩距、退刀槽和倒角尺寸 207
2.普通内螺纹收尾、肩距、退刀槽和倒角尺寸 208
3.米制锥螺纹(内螺纹)收尾和退刀槽尺寸 209
三、车削螺纹时挂轮的计算 209
1.挂轮形式和啮合要求 211
2.挂轮计算公式及实例 211
3.车削特殊螺距螺纹时挂轮的计算 212
(1)车削非标准螺距时挂轮的计算 212
(2)车削模数蜗杆或径节蜗杆时挂轮的计算 214
(3)根据螺旋导程计算挂轮 214
4.π的近似分数值 215
四、螺纹车刀的几何参数及螺纹切削图形 216
1.螺纹车削的方法与切削图形 216
2.螺纹车刀顶刃宽度的计算 217
(1) 30°梯形螺纹车刀的顶刃宽度尺寸 217
(2) 40°模数蜗杆车刀的顶刃宽度尺寸 218
(3) 29°径节蜗杆车刀的顶刃宽度尺寸 218
3.螺纹车刀两侧刃后角的计算 219
4.螺纹车刀前角对牙型角的影响 220
五、车削多线螺纹的分线方法 221
1.概述 221
2.轴向分线法 221
3.圆周分线法 222
(1)挂轮分线法 223
(2)利用简易分度盘分线 223
六、车削蜗杆的方法 223
1.车削圆柱形模数蜗杆 223
2.公制蜗杆各部分尺寸计算 225
七、车削不等距螺杆 226
1.不等距螺杆装置的结构原理 226
2.注意事项 227
八、内螺纹的加工方法 228
1.采用丝锥攻螺纹 228
(1)丝锥的形状 228
(2)丝锥的种类 228
(3)底孔钻头直径的选择 229
2.用丝锥攻内螺纹的方法 232
3.采用梯形内螺纹拉削丝锥简介 232
(1)概述 232
(2)拉削丝锥的几何参数 233
(3)操作说明 234
九、几种高效率螺纹车刀 234
1.可转位螺纹车刀 234
2.机夹式高效螺纹车刀 235
3.可转位精密螺纹车刀 236
十、旋风切削螺纹 237
1.旋风切削的概念 237
(1)逆切法 238
(2)顺切法 238
2.旋风切削用量及有关问题 239
(1)切削用量的选择 239
(2)旋刀刀尖旋转直径与螺纹直径比的选择 240
(3)旋风切削的切削功率 240
(4)圆球螺杆的旋风切削 241
十一、螺纹滚压加工 243
1.概述 243
2.滚压螺纹的主要方法及应用范围 243
3.滚压不同材料、不同硬度螺纹的工艺直径 245
十二、螺纹的常用测量方法 246
1.单项测量法 246
(1)顶径的测量 247
(2)螺距的测量 247
(3)螺纹牙型的测量 247
(4)中径的测量 247
(5)蜗杆齿厚的测量 247
2.综合测量法 248
3.带镀层的螺纹镀前加工的测量法 249
4.三针测量螺纹中径法 249
(1)计算公式 249
(2)测量普通螺纹时的M值 251
(3)测量梯形螺纹时的M值 254
十三、车削螺纹时产生缺陷与故障的原因及预防措施 255
十四、螺纹的基本尺寸及其公差 256
1.普通螺纹 256
(1)米制普通螺纹 256
(2)统一标准螺纹 266
(3)惠氏螺纹 269
2.管螺纹 271
(1)英制密封管螺纹 271
(2)英制非密封管螺纹 273
(3)米制管螺纹 275
3.梯形螺纹 277
4.锯齿形螺纹 287
第四章 孔加工 295
一、钻削 296
1.标准麻花钻 296
(1)标准麻花钻的组成 296
(2)标准麻花钻切削部分的组成 297
(3)标准麻花钻的三个辅助平面 298
(4)标准麻花钻的几何参数 298
2.钻削用量 300
(1)钻削用量的计算 300
(2)钻削用量的推荐值 302
3.标准麻花钻的优缺点及改进措施 303
(1)优点 303
(2)缺点 303
(3)标准麻花钻的修磨措施 304
(4)钻孔时产生缺陷的原因及防止方法 305
4.其他几种钻头 305
(1)分屑槽钻头 305
(2)硬质合金钻头 306
(3)斜面钻 306
(4)半孔钻 306
(5)球形万向钻 307
(6)几种精确扩孔钻 307
(7)平底孔钻 309
(8)多刃带阶梯钻 309
(9)方孔钻 309
(10)扁钻 311
(11)群钻 313
二、锪削 321
1.锪钻的尺寸 321
2.机夹硬质合金锪钻 325
三、铰削 325
1.铰削特点 325
2.铰削用量的推荐值 326
3.铰刀的结构 327
4.介绍几种铰刀 329
(1)可调节手用铰刀 329
(2)斜齿套式机用铰刀 329
(3)大刃倾角铰刀 330
(4)小深孔双刃拉铰刀 330
(5)月牙形铰刀 331
(6)锥销孔校正铰刀 331
(7)阶梯形铰刀 332
(8)少齿数螺旋形铰刀 332
(9)跳齿螺旋形铰刀 333
(10)大螺旋角铰刀 333
(11)硬质合金铰刀 334
(12)硬质合金斜齿铰刀 335
(13)套式硬质合金饺刀 335
(14)小粗糙度可调节硬质合金铰刀 336
(15)无刃铰刀 337
(16)硬质合金机夹无刃铰刀 338
(17)硬质合金盲孔无刃铰刀 338
5.高速铰孔用旋转导套 339
(1)滚珠式旋转导套 339
(2)滚针式旋转导套 340
6.夹持铰刀的浮动装置 340
7.铰削用量的推荐值 342
8.铰孔中常见缺陷及解决措施 343
四、镗削 345
1.镗床基本工作范围 345
2.镗刀种类 346
3.介绍几种镗刀 346
(1)装夹式可调单刃镗刀 346
(2)微调镗刀 347
(3)微型机夹式精镗刀 347
(4)刚性镗铰刀 350
4.镗头及镗排 351
(1)横向微动镗头 351
(2)差动镗刀排 353
(3)差动微调镗排 353
(4)精密微调镗排 354
(5)旋转封闭式可调镗排 355
(6)内球面自动进给镗排 355
(7)可调组合镗排 356
(8)内球面镗排 357
(9)锥孔镗排 357
五、深孔加工 358
1.概述及深孔加工的特点 358
(1)概述 358
(2)深孔加工的特点 358
2.深孔钻削 359
(1)单刃外排屑深孔钻 359
(2)单管内排屑深孔钻 368
(3)喷吸钻 376
(4) DF深孔钻削系统 381
(5)深孔套料 382
3.深孔镗(扩)孔 392
(1)镗孔方式的选择 392
(2)深孔镗刀的设计要点 394
(3)装夹式推镗刀 398
(4) SANDVIK公司T-MAX 424.31F及424.31深孔扩孔钻 398
(5)离心浇铸管拉镗刀 406
4.深孔铰削 406
(1)深孔铰削的特点 406
(2)深孔铰刀的几何参数选择 407
(3)单刃深孔铰刀 409
(4)焊接式硬质合金拉铰刀 409
(5)自导向深孔镗铰刀 411
(6)浮动铰刀 412
5.深孔滚压 415
(1)深压加工的原理及特点 415
(2)深孔滚压的滚压元件及选择 415
(3)典型滚压工具 417
6.深孔珩磨 421
(1)珩磨加工及特点 421
(2)珩磨方式 423
(3)珩磨工具的结构 424
(4)珩磨油石的选择及修整 427
(5)珩磨工艺参数 432
(6)常见珩磨缺陷及解决措施 434
第五章 拉削 437
一、拉削的加工范围与特点 437
1.加工范围 437
2.拉削特点 438
二、拉刀的种类及组成 439
1.常用拉刀种类 439
2.拉刀的组成 440
三、拉削方式及切削层几何参数 441
1.拉削方式 441
2.切削层几何参数 442
四、拉刀各部分尺寸 442
1.拉刀切削部分的几何参数名称 442
2.拉刀齿升量fz 443
3.齿距p 444
4.拉刀几何角度的选择 444
(1)拉刀前角γo的选择 444
(2)拉刀后角αo与刃带bα的选择 445
5.拉刀容屑槽的形状与尺寸 445
(1)容屑槽尺寸的计算 445
(2)拉刀容屑槽的容屑系数K 445
(3)直线齿背容屑槽的形状与尺寸 446
(4)曲线齿背容屑槽的形状与尺寸 447
6.拉刀分屑槽的形状与尺寸 448
(1)圆孔拉刀弧形分屑槽的形状与尺寸 448
(2)圆孔拉刀V分屑槽的形状与尺寸 449
(3)平面拉刀分屑槽的形状与尺寸 449
(4)花键、键槽拉刀分屑槽的形状与尺寸 450
7.拉刀前导部、后导部的形状与尺寸 450
(1)前导部的形状与尺寸 450
(2)后导部的形状与尺寸 451
8.拉刀柄部的形式与尺寸 452
(1)柄部长度的决定 452
(2)内孔拉刀的圆柱形前柄 453
(3)键槽拉刀的矩形柄部 455
五、拉刀的技术条件 456
1.表面粗糙度 456
2.尺寸偏差 457
(1)拉刀外圆在全长上允许的最大径向圆跳动量 457
(2)拉刀切削齿外圆直径偏差 457
(3)拉刀校准齿直径偏差 457
(4)花键拉刀键齿不等分累积误差 458
(5)键槽拉刀切削齿齿高偏差 459
六、拉削余量的推荐值 459
1.圆孔拉削余量 459
2.多边形孔拉削余量 460
七、拉削力的计算与拉刀强度验算 460
1.拉削力的计算 460
(1)计算公式 460
(2)单位长度切削刃上的切削力 461
2.拉刀强度验算 461
八、拉削前的工艺准备 461
1.拉削前对工件的工艺要求 461
2.拉削速度的选取 462
3.拉床允许拉力的验算 462
九、拉刀的合理使用与修复工艺 463
1.拉刀的合理使用 463
2.拉刀的修复 464
(1)拉刀折断后的修复方法 464
(2)拉刀直径变小后的修复方法 464
(3)拉刀上个别刀齿崩刃后的修复方法 465
(4)拉刀校准齿严重磨损后的修复方法 465
3.拉削时常见的缺陷及解决方法 465
十、拉削加工的应用特例——螺旋油槽的加工 468
十一、内齿轮拉削 470
第六章 刨削 473
一、刨削加工范围及特点 473
1.加工范围 473
2.刨削特点 473
二、刨削用量 474
1.刨削用量要素的定义及计算公式 474
2.刨削用量的选择 475
(1)切削深度ap的选择 475
(2)进给量f的选择 475
(3)切削速度υc的选择 475
三、刨削时常用的几种装夹方法 480
四、介绍几种刨刀 481
1.机夹大前角和大刃倾角刨刀 481
2.强力割刀 482
3.圆形刨刀 483
4.宽刃精刨刀 483
5.可调式精刨刀 484
6.机夹后压式刨刀 485
五、介绍几种工具与刨削方法 486
六、典型零件的刨削 487
1.刨薄板工件 487
(1)加工特点及使用刀具 487
(2)工件的装夹及刨削方法 488
2.刨T形槽 489
(1) T形槽的各部分尺寸 489
(2) T形槽的加工特点 489
(3)刨T形槽的刀具 490
(4)刨削方法 490
(5)刨T形槽的注意事项 490
3.刨V形槽 491
(1) V形槽的刨削方法 491
(2) V形槽的测量 491
4.刨斜镶条 492
(1)斜镶条的加工特点 492
(2)斜镶条的毛坯尺寸计算 492
(3)斜镶条的刨削方法 493
5.刨燕尾形工件 493
(1)燕尾形工件的加工特点及各部尺寸关系 493
(2)刨燕尾形工件的刀具 494
(3)燕尾形工件的刨削方法 494
(4)刨斜燕尾时的调整计算 495
七、曲面的刨削方法 496
1.刨削内外圆弧型面 496
2.龙门刨刨削大半径圆弧 497
3.龙门刨自动进给刨内圆弧型面 497
4.牛头刨靠模刨曲面 497
5.龙门刨光电靠模仿形刨曲面 498
第七章 铣削 501
一、铣削加工范围 501
二、铣刀 502
1.铣刀主要几何参数的数值 502
(1)高速钢铣刀的几何参数参考值 502
(2)硬质合金面铣刀的几何参数参考值 503
2.铣刀主要结构参数的选择 503
(1)铣刀直径的选择 503
(2)铣刀齿数的选择 504
3.常用标准铣刀的用途、规格及主要参数 505
(1)立铣刀 505
(2)键槽铣刀 514
(3)圆柱形铣刀 518
(4)面铣刀 518
(5)三面刃铣刀 520
(6)锯片铣刀 524
(7) T形槽铣刀 527
(8)半圆键槽铣刀 528
(9)半圆铣刀及圆角铣刀 528
(10)角度铣刀 529
(11)模具铣刀 532
4.介绍几种铣刀 539
三、铣削用量 543
1.铣削用量要素的定义及计算公式 543
2.铣削用量的选择 545
(1)铣削深度ap的选择 545
(2)每齿进给量fz的选择 545
(3)铣削速度υc的选择 549
四、分度头及其应用 550
1.简介 550
2.分度头的应用 551
(1)单式分度法 551
(2)角度分度法 554
(3)差动分度法 568
(4)直线移距分度法 571
(5)利用分度头加工螺旋槽的挂轮计算和配置方法 574
(6)小导程工件的挂轮计算和配置方法 576
(7)大导程工件的挂轮计算和配置方法 578
(8)速比和导程挂轮表 581
五、铣齿键 591
1.单刀铣花键 591
(1)工件的装夹和校正 592
(2)铣刀的选择和安装 592
(3)对刀 592
(4)铣键侧和槽底 594
2.组合铣刀铣花键 595
(1)用组合三面刃铣刀铣花键 595
(2)用硬质合金组合刀盘精铣花键 595
3.成形铣刀铣花键 596
4.花键铣削时常见的弊病及防止方法 598
六、铣离合器 599
1.矩形齿离合器的加工计算 99
(1)铣偶数齿离合器 599
(2)铣奇数齿离合器 599
(3)铣刀宽度和直径的确定 601
2.尖齿和梯形收缩齿离合器的加工计算 601
3.锯齿形齿离合器的加工计算 602
七、铣弧形面 603
1.球面的加工计算 603
(1)铣带柄圆球 603
(2)铣内球面 604
(3)铣大半径球面 605
2.椭圆孔和椭圆面的加工计算 607
(1)加工原理 607
(2)加工实例 607
(3)镗椭圆孔时刀杆直径的确定 607
(4)铣内椭圆面 608
3.大半径圆弧面的近似加工计算 608
八、铣等速圆盘凸轮 609
1.平面螺旋线的形成及特点 609
2.铣阿基米德螺旋线凸轮 609
(1)凸轮导程的计算 609
(2)垂直铣削法 610
(3)倾斜铣削法 612
九、铣刀与铰刀的开齿 614
1.圆柱面直齿槽的开齿计算 614
(1)用单角铣刀开齿槽 614
(2)用双角铣刀开齿槽 615
(3)已知棱边宽度时齿槽深度的计算 617
(4)铣第二重后刀面 618
2.划线开齿法 619
3.圆柱面螺旋齿槽的开齿计算 620
(1)铣螺旋槽时的干涉 620
(2)工作铣刀及其旋转方向的确定 622
(3)工作台转角的确定 623
(4)铣刀与工件相对位置的确定 624
(5)常见圆柱形螺旋齿刀具的开齿 629
(6)圆柱面螺旋齿槽铣削时常见弊病及原因 631
4.端面齿槽的开齿计算 631
(1)直齿刀具端面齿槽的开齿计算 631
(2)螺旋齿刀具端面齿槽的开齿计算 632
5.锥面直齿槽的开齿计算 633
(1)角度铣刀的锥面直齿槽开齿计算 633
(2)前角γo=0°的直齿锥度铰刀的开齿计算 634
(3)前角γo>0°的直齿锥度铰刀的开齿计算 636
第八章 齿轮加工 637
一、圆柱齿轮传动 637
1.标准直齿圆柱齿轮各部分名称及代号 637
2.标准直齿圆柱齿轮主要名词解释 637
3.齿轮模数系列 638
4.渐开线圆柱齿轮基本齿廓 639
5.标准直齿圆柱齿轮传动计算 639
(1)几何尺寸计算 639
(2)齿厚测量 640
6.标准斜齿圆柱齿轮各部分名称及代号 647
7.标准斜齿圆柱齿轮主要名词解释 647
8.标准斜齿圆柱齿轮传动计算 648
(1)平行轴斜齿圆柱齿轮传动计算 648
(2)交叉轴斜齿圆柱齿轮传动计算 650
9.变位齿轮基本知识 651
(1)变位齿轮概述 652
(2)变位齿轮与标准齿轮的主要区别 652
(3)变位方法的选择 653
(4)不产生根切的最少齿数 653
10.高度变位直齿圆柱齿轮传动计算 653
(1)几何尺寸计算 653
(2)齿厚测量 654
11.角度变位直齿圆柱齿轮传动计算 656
12.高度变位斜齿圆柱齿轮传动计算 657
13.角度变位斜齿圆柱齿轮传动计算 658
二、锥齿轮传动 660
1.锥齿轮传动各部名称及代号 660
2.直齿锥齿轮传动计算 661
(1)直齿锥齿轮几何尺寸计算 661
(2)非变位直齿锥齿轮分度圆弦齿厚及测量用齿高 663
三、圆柱形蜗杆蜗轮传动 664
1.圆柱形蜗杆蜗轮传动计算 664
(1)圆柱形蜗杆蜗轮各部分名称及代号 664
(2)圆柱形蜗杆蜗轮各部分尺寸计算 665
(3)蜗杆分度圆柱上的法向弦齿厚-sn1及测量用齿高-hnl 667
2.圆柱形蜗杆传动的主要参数 667
(1)蜗杆轴向模数mx和蜗杆直径系数q 667
(2)蜗杆在分度圆柱上的螺纹升角λ1 668
(3)蜗杆螺纹部分长度L 668
(4)蜗杆头数z1与蜗轮齿数z2的推荐值 669
四、齿轮加工常用方法 669
五、铣齿轮 671
1.铣直齿圆柱齿轮的盘铣刀 671
2.铣斜齿圆柱齿轮 672
(1)铣刀刀号的选择 672
(2)挂轮计算 675
3.铣齿条 675
(1)铣直齿条的移距方法 676
(2)铣斜齿条的移距方法 679
4.铣直齿锥齿轮 679
(1)锥齿轮铣刀及其刀号的选择 679
(2)直齿锥齿轮的加工方法及计算 380
5.用一刀成形法铣直齿锥齿轮 686
(1)加工原理 686
(2)加工方法 687
六、滚齿加工 689
1.齿轮滚刀 689
(1)齿轮滚刀的实质和近似造形 689
(2)齿轮滚刀的精度等级 689
(3)剃前滚刀和磨前滚刀 689
(4)多头滚刀 689
(5)正前角滚刀 690
2.滚齿工作 693
(1) Y3150E型滚齿机 693
(2) Y3150E型滚齿机及常用滚齿机分齿挂轮与差动挂轮计算 697
(3)滚切齿数大于100的质数齿轮的挂轮计算 699
(4)滚齿机加工圆柱齿轮时应注意的问题 703
(5)蜗轮加工 707
(6)滚齿时产生缺陷的原因与消除方法 708
七、插齿加工 710
1.插齿刀 710
2.Y54型插齿机的传动系统 716
3.插直齿圆柱外齿轮 716
(1)插齿刀行程长度的决定 716
(2)切削速度的调整 717
(3)分齿交换齿轮的选择 718
(4)圆周进给交换齿轮的选择 718
(5)径向进给的方式及其调整方法 723
4.插直齿圆柱内齿轮 724
(1)工件的安装 725
(2)插齿刀的验算 725
(3)内齿轮齿厚的测量 725
5.插齿条 727
(1)插齿机的改装 727
(2)分齿挂轮计算 727
(3)分齿挂轮表 729
6.插齿加工常见超差原因及纠正措施 729
八、剃齿加工 731
1.剃齿刀 731
(1)剃齿刀的结构 731
(2)标准盘形剃齿刀的规格尺寸 732
2.剃齿方法及剃齿刀与工件的安装角 733
3.剃前齿形及剃前刀具 734
4.剃齿余量 735
5.改善“剃齿中凹”的方法 736
(1)实验误差补偿修形法 736
(2)随机修形法 738
九、直齿锥齿轮刨齿加工 738
1.直齿锥齿轮刨齿的工作原理及刨齿刀 738
(1)直齿锥齿轮刨齿的工作原理 738
(2)标准直齿锥齿轮刨齿刀 739
2.Y236型直齿锥齿轮刨齿机的传动系统 744
3.Y236型刨齿机的挂轮计算 745
4.Y236型刨齿机的挂轮表 746
(1)刨刀往复行程挂轮 746
(2)进给挂轮 746
(3)转盘(摇台)摆动角度 746
(4)转盘(摇台)摆动角度系数值Mθ 747
(5)分齿挂轮(适用于单分齿法) 748
5.刨齿刀滑板导轨夹角调整 749
(1)单分齿法时按齿角调整 749
(2)双分齿法时按齿角调整 751
6.按根锥角δf调整分齿箱回转台安装角 751
7.加工余量与轴向移动量ΔL′关系 751
(1) α=20°和△s=0.1时齿轮轴线的移动量ΔL′ 752
(2)利用曲线图求齿轮轴线移动量ΔL′ 752
8.应用举例 754
(1)用双分齿法粗刨大齿轮 754
(2)单分齿法精刨大齿轮 755
(3)用单分齿法粗刨小齿轮 755
(4)精刨小齿轮 756
9.齿面修正 757
(1)齿向接触 757
(2)齿面接触 758
第九章 磨削 769
一、磨削的基本概念 769
1.常见的磨削方式 769
2.磨削加工的特点 771
3.磨削要素 772
(1)磨削速度υc 772
(2)工件速度υw 772
(3)磨削深度或径向进给量fr 773
(4)轴向进给量fa 773
(5)材料切除率Q 773
(6)磨削比G 773
二、磨具 773
1.砂轮的组成及标志 773
2.砂轮的特性及选择 774
(1)磨料的特性及选择 774
(2)磨料的粒度及选择 775
(3)结合剂及选择 776
(4)砂轮的硬度及选择 777
(5)砂轮的组织及选择 778
(6)砂轮的形状及尺寸的选择 779
(7)砂轮的安全速度 781
3.砂轮的平衡 783
(1)砂轮平衡的方法 783
(2)砂轮调整静平衡时的注意事项 783
4.砂轮的修整方法与工具 784
(1)砂轮的修整方法 784
(2)砂轮的修整工具及其选用 784
(3)修整砂轮时的注意事项 787
5.砂轮的安全使用 788
三、磨削工艺参数及磨削液 789
1.砂轮的修整用量 789
(1)砂轮的修整导程f 789
(2)修整时径向进给量的选择 789
(3)砂轮径向的修整总量 789
2.砂轮成形修整的方法及工艺 789
(1)成形修整方法 789
(2)成形修整工艺 792
3.磨削用量的选择 793
(1)砂轮速度υc 794
(2)工件速度υw 794
(3)砂轮轴向进给量fa 794
(4)磨削深度fr 794
(5)光磨次数 794
4.磨削液及砂轮表面冲洗 795
(1)磨削液的主要作用 795
(2)磨削液的选用 795
(3)磨削液的使用要点 796
(4)磨削液的过滤方法 796
(5)砂轮表面冲洗 798
四、磨削加工中常见的缺陷及消除措施 799
1.外圆磨削中常见的缺陷及消除措施 799
2.内圆磨削中常见的缺陷及消除措施 802
3.平面磨削中常见的缺陷及消除措施 804
4.无心外圆磨削中常见的缺陷及消除措施 806
5.其他磨削中常见的缺陷及消除措施 809
(1)双端面磨削中常见的缺陷及消除措施 809
(2)曲轴磨削中常见的缺陷及消除措施 809
(3)凸轮轴磨削中常见的缺陷及消除措施 810
(4)花键磨削中常见的缺陷及消除措施 810
(5)导轨磨削中常见的缺陷及消除措施 810
五、高精度小粗糙度磨削 811
1.高精度小粗糙度磨削的加工特点 811
2.高精度小粗糙度磨削的应用范围 811
3.小粗糙度表面的形成 812
4.小粗糙度磨削的砂轮选择 812
5.高精度小粗糙度磨削对机床的要求 813
6.小粗糙度高精度磨削工艺参数的选择 814
(1)外圆小粗糙度高精度磨削工艺参数的选择 814
(2)内圆小粗糙度高精度磨削工艺参数的选择 814
(3)平面小粗糙度高精度磨削工艺参数的选择 815
(4)无心外圆小粗糙度高精度磨削工艺参数的选择 816
7.加工实例 816
(1)磨床主轴 816
(2)测量主轴锥孔径向圆跳动的锥尾试棒 818
(3)莫氏环规的内孔加工 818
(4)精密滚柱轴承外环的内孔磨削 820
(5)静压轴承节流器薄膜片的磨削 821
(6)精密刻线尺的尺面磨削 822
(7)大平面的磨削 822
六、高速磨削 824
1.高速磨削的加工特点 826
2.对50~60 m/s高速外圆磨床的要求 826
(1)砂轮电动机功率的选择 826
(2)砂轮主轴轴承 826
(3)磨削液的流量与压力 826
(4)磨削液喷嘴 827
(5)砂轮罩 827
(6)其他方面 827
3.高速磨削的工艺参数 828
七、深切缓进磨削 828
1.深切缓进强力磨削的主要特点 829
2.深切缓进磨削对机床的要求 829
3.深切缓进磨削的砂轮选择 830
4.深切缓进强力磨削的工艺参数 831
5.加工实例 831
(1)燃气轮机叶片根槽的成形磨削 831
(2)三爪卡盘卡爪导向槽的成形磨削 832
八、宽砂轮磨削 832
1.宽砂轮磨削的特点 832
2.宽砂轮磨削对磨床的要求 833
3.宽砂轮磨削的砂轮 833
4.宽砂轮磨削工艺参数的选择 834
(1)工件速度的选择 834
(2)切入进给速度的选择 834
(3)光磨时间的选择 834
(4)精密磨削的工艺参数 835
5.加工实例 835
(1)磨削冷打花键外圆及双曲线轧辊 835
(2)宽砂轮磨削滑阀阀芯 835
九、超硬磨料砂轮磨削 836
1.超硬磨料砂轮的结构及磨削特点 837
2.超硬磨料砂轮的特性的选择 837
(1)磨料的选择 837
(2)粒度的选择 838
(3)结合剂的选择 839
(4)浓度的选择 839
(5)硬度的选择 840
(6)超硬磨料砂轮的形状和选用 840
3.金刚石砂轮磨削用量的选择 841
(1)砂轮速度的选择 841
(2)磨削切深的选择 841
(3)工件线速度的选择 842
(4)进给速度的选择 842
(5)磨削液的选择 842
4.金刚石砂轮的修整 842
(1)金刚石砂轮修整的必要性 842
(2)金刚石砂轮的修整方法 843
(3)用普通磨料的砂轮修整金刚石砂轮的工艺 843
5.金刚石砂轮使用时的注意事项 844
6.金刚石研磨膏的选用 844
7.立方氮化硼砂轮的特点及应用 845
(1)立方氮化硼砂轮的磨削特点 845
(2)立方氮化硼砂轮的加工实例 845
十、难磨材料的磨削及难磨零件的磨削加工 846
1.难磨材料的磨削加工 846
(1)难磨削材料的概念 846
(2)解决难磨材料磨削问题的途径 846
2.几种难磨零件的磨削加工 847
(1)细长轴的磨削 847
(2)薄壁套筒的外圆磨削 848
(3)薄片零件的平面磨削 848
(4)深孔的磨削 849
第十章 刀具的刃磨 851
一、刀具刃磨的设备 851
1.刀具刃磨设备的分类、特点和适用范围 851
2.万能工具磨床的主要附件及用途 851
3.万能工具磨床的常用工具及用途 853
二、砂轮的选择及修整 855
1.砂轮的形状及外径的选择 855
2.砂轮的特性选择 856
(1)一般砂轮的特性选择 856
(2)刃磨硬质合金刀具的金刚石砂轮的特性选择 857
3.砂轮的修整 858
三、铣刀及铰刀的刃磨 858
1.刃磨几何参数及刃磨精度要求 858
2.刃磨方法及有关调整计算 865
四、拉刀的刃磨 872
1.拉刀的刃磨要求 872
2.刃磨方法及砂轮直径的选择 872
(1)用砂轮锥面刃磨 872
(2)用砂轮外圆刃磨 873
五、插齿刀的刃磨 874
1.插齿刀的刃磨方法 874
2.砂轮直径的选择 874
3.插齿刀的刃磨要求 876
六、齿轮滚刀及蜗轮滚刀的刃磨 876
1.齿轮滚刀及蜗轮滚刀的刃磨精度要求 876
2.齿轮滚刀及蜗轮滚刀的刃磨方法 877
第十一章 数控技术在切削加工中的应用 881
一、数控加工技术基础 881
1.数控机床的基本知识 881
(1)数控机床的加工过程 881
(2)数控机床的组成 881
(3)数控机床的伺服控制方式 883
(4)数控机床的运动控制方式 884
(5)几种常用数控机床的功能及结构特点 885
2.数控机床加工的特点及适用范围 887
3.数控机床的坐标系 888
(1)定义坐标系的原则 888
(2)典型数控机床的坐标轴及运动方向 888
(3)机床坐标系 890
(4)工件坐标系 890
(5)绝对坐标与增量(相对)坐标 890
(6)可控轴数及多轴联动 891
二、数控刀具及工具系统 891
1.数控加工对刀具的要求及选择 891
(1)对刀具材料的要求 891
(2)对刀具的精度要求 892
(3)对刀具的结构要求 892
(4)数控刀具的系列化、标准化及通用化 893
2.数控工具系统 893
(1)镗铣类数控机床与工具系统的接口 893
(2)镗铣类数控机床的整体式工具系统 895
(3)镗铣类数控机床的模块式工具系统 899
(4)车削类数控机床的工具系统 905
3.数控刀具的预调 909
(1)刀具尺寸的调整方法 910
(2)刀具尺寸预调的要求 911
(3)典型的对刀装置(仪) 912
4.刀库及自动换刀装置 914
(1)刀库的类型 914
(2)自动换刀装置 915
(3)自动换刀时刀具的选择方式 916
三、数控加工工艺制定 918
1.数控加工的工艺特点 918
2.数控工艺制定中的若干问题 918
(1)零件图的分析及必要的数学处理 918
(2)数控工序的划分 920
(3)走刀路线的确定 920
(4)对刀点和换刀点的确定 925
(5)工艺文件的编制 926
3.典型零件的数控加工工艺 928
(1)轴类零件的数控车削加工工艺 928
(2)平面凸轮的数控铣削加工工艺 931
(3)异形支架的加工中心加工工艺 933
四、数控程序编制 937
1.数控程序编制的步骤及方法 937
(1)编程步骤 937
(2)编程方法 938
2.数控程序的编制格式 939
(1)数控程序的结构 939
(2)程序段的格式 939
3.数控程序常用功能指令 940
(1)准备功能G指令及应用 940
(2)辅助功能M指令及应用 951
(3)工艺性指令 952
4.车削类数控机床的固定循环指令 952
(1)单一固定循环指令 953
(2)多重复合循环指令 956
5.镗铣类数控机床的孔加工固定循环指令 960
(1)孔加工的基本动作 960
(2)孔加工固定循环指令的一般格式 961
(3)孔加工固定循环指令及应用 961
6.子程序的应用 967
(1)子程序的编程格式 968
(2)子程序的调用及嵌套 968
(3)子程序的应用示例 968
7.宏程序的应用 970
(1)宏程序的概念 970
(2)变量与赋值 970
(3)算术运算和逻辑运算 972
(4)转移和循环 972
(5)宏程序的调用 973
(6)宏程序的应用示例 974
8.数控编程实例 975
(1)编程实例一 975
(2)编程实例二 977
附录1物理量单位及其换算 981
一、法定计量单位 981
1.国际单位制的基本单位及辅助单位 981
2.国际单位制中具有专门名称的导出单位 981
3.国家规定的非国际单位制单位 982
4.用于构成十进倍数和分数单位的词头 983
二、物理量单位的换算 983
1.长度单位换算 983
2.面积单位换算 983
3.体积、容积单位换算 984
4.质量单位换算 984
5.密度单位换算(20℃) 984
6.线速度单位换算 985
7.角速度单位换算 985
8.力的单位换算 985
9.压力、压强、应力单位换算 986
10.功、能及热量单位换算 986
11.功率单位换算 987
12.比热容单位换算 987
13.热导率单位换算 987
三、钢材的硬度与强度近似换算 988
附录2公差配合及表面粗糙度 993
一、公差配合 993
1.新、旧国标的公差代号对照(尺寸1~500 mm) 993
2.轴的常用偏差(尺寸1~500 mm) 995
3.孔的常用偏差(尺寸1~500 mm) 1012
二、几何公差 1029
1.几何公差的符号及标注 1029
2.几何公差值 1030
(1)直线度、平面度 1030
(2)圆度、圆柱度 1031
(3)平行度、垂直度、倾斜度 1032
(4)同轴度、对称度、圆跳动和全跳动 1034
三、表面粗糙度 1036
1.表面粗糙度的常用评定参数及数值 1036
2.旧标准表面光洁度代号与第1系列的表面粗糙度代号对照参考表 1038
3.表面粗糙度与零件公差等级的关系 1038
附录3国内外金属材料牌号对照 1039
一、钢铁材料 1039
1.碳素结构钢钢号近似对照 1039
2.优质碳素结构钢钢号近似对照 1040
3.合金结构钢钢号近似对照 1042
4.易切削结构钢钢号近似对照 1046
5.弹簧钢钢号近似对照 1047
6.轴承钢钢号近似对照 1048
7.不锈钢钢号近似对照 1049
8.耐热钢钢号近似对照 1054
9.工具钢钢号近似对照 1057
10.碳素铸钢及合金铸钢钢号近似对照 1061
11.不锈铸钢及耐蚀铸钢钢号近似对照 1062
12.耐热铸钢钢号近似对照 1063
13.高锰铸钢钢号近似对照 1064
14.承压铸钢钢号近似对照 1064
15.灰铸铁牌号近似对照 1065
16.球墨铸铁牌号近似对照 1066
17.可锻铸铁牌号近似对照 1066
18.抗磨铸铁牌号近似对照 1068
二、高温合金及耐蚀合金 1068
1.变形高温合金牌号近似对照 1068
2.铸造高温合金牌号近似对照 1073
3.耐蚀合金牌号近似对照 1074
三、有色金属材料 1075
1.铜合金牌号近似对照 1075
2.铝合金牌号近似对照 1082
3.锌合金牌号近似对照 1088
四、硬质合金 1089
附录4金属材料的热处理 1092
一、钢材材料的热处理 1092
1.钢铁金相组织的名称和特性 1092
2.钢铁的主要热处理方法 1093
3.常用钢材的热处理规范 1094
4.钢材热处理变形的一般趋向 1101
5.灰铸铁的热处理规范 1101
二、有色金属的热处理 1102
1.铜合金的常用热处理 1102
2.铝合金的常用热处理 1103
3.钛合金的常用热处理 1104
附录5硬质合金刀片的规格尺寸 1106
一、普通硬质合金刀片 1106
1.硬质合金焊接刀片 1106
2.内排屑深孔钻用硬质合金刀片 1115
二、硬质合金可转位刀片 1117
1.带圆孔的硬质合金可转位刀片 1117
2.无孔的硬质合金可转位刀片 1138
3.沉孔硬质合金可转位刀片 1141
4.硬质合金可转位铣刀片 1148
- 《Maya 2018完全实战技术手册》来阳编著 2019
- 《高等教育双机械基础课程系列教材 高等学校教材 机械设计课程设计手册 第5版》吴宗泽,罗圣国,高志,李威 2018
- 《慢性呼吸系统疾病物理治疗工作手册》(荷)瑞克·考斯林克(RikGosselink) 2020
- 《战略情报 情报人员、管理者和用户手册》(澳)唐·麦克道尔(Don McDowell)著 2019
- 《实用内科手册》黄清,阮浩航主编 2016
- 《基层医疗卫生机构安全用药手册》黎月玲,熊慧瑜 2019
- 《同仁眼科手册系列 同仁儿童眼病手册》付晶编 2018
- 《环境噪声监测实用手册》中国环境监测总站编 2018
- 《高度关注物质(SVHC)毒性手册 上》顾爱华主编 2019
- 《吉他宝典 吉他手超级手册 上》姜伟主编;汶麟,姚林,杜新春,赖康康,朱家明,克尔曼副主编 2018
- 《大学化学实验》李爱勤,侯学会主编 2016
- 《在生活中养生 《中国公民中医养生保健素养》解读》吕沛宛,侯江红 2019
- 《中国奇迹与意识形态》郭忠义,侯亚楠著 2018
- 《香山设县850年》吴冉彬主编;中山市地方志办公室等编 2003
- 《2017国家执业药师资格考试辅导教材 药学综合知识与技能》侯晨辉,王莹 2017
- 《晚霞风景 《晚霞》杂志创刊十周年作品选集》王诚德等编 1999
- 《骨折鉴别诊断学》张英泽主编;侯志勇,孙英彩,张泽坤,吴文娟副主编 2018
- 《行知工程创新教学探索系列 小学语文单元整体课程实施与评价》李怀源等编 2012
- 《诗文阅读入门》邵霭吉,戴永俊,朱桂元主编;王延潭,王学荣,王辉等编 1991
- 《全国精美作文年选 2009年度经典 高中卷》邵荣霞主编;邵荣霞,张年军,屠丽君等编 2010
- 《钒产业技术及应用》高峰,彭清静,华骏主编 2019
- 《现代水泥技术发展与应用论文集》天津水泥工业设计研究院有限公司编 2019
- 《异质性条件下技术创新最优市场结构研究 以中国高技术产业为例》千慧雄 2019
- 《Prometheus技术秘笈》百里燊 2019
- 《中央财政支持提升专业服务产业发展能力项目水利工程专业课程建设成果 设施农业工程技术》赵英编 2018
- 《药剂学实验操作技术》刘芳,高森主编 2019
- 《林下养蜂技术》罗文华,黄勇,刘佳霖主编 2017
- 《脱硝运行技术1000问》朱国宇编 2019
- 《催化剂制备过程技术》韩勇责任编辑;(中国)张继光 2019
- 《信息系统安全技术管理策略 信息安全经济学视角》赵柳榕著 2020