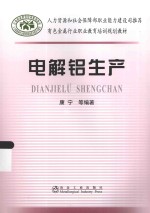
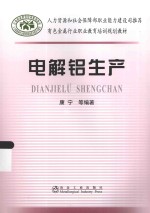
电解铝生产PDF电子书下载
- 电子书积分:13 积分如何计算积分?
- 作 者:康宁编著
- 出 版 社:北京:冶金工业出版社
- 出版年份:2015
- ISBN:9787502469092
- 页数:396 页
1 铝电解生产概论 1
1.1 铝工业发展简史 1
1.1.1 化学法炼铝 1
1.1.2 电解法炼铝 1
1.2 铝的性质及用途 2
1.2.1 铝的性质 2
1.2.2 铝的用途 3
1.3 铝电解生产工艺流程 4
1.4 铝电解生产所用的原材料 4
1.4.1 氧化铝 5
1.4.2 冰晶石 6
1.4.3 氟化铝 6
1.4.4 氟化钠 7
1.4.5 氟化钙 7
1.4.6 氟化镁 7
1.4.7 氟化锂 8
1.4.8 阳极炭块 8
1.4.9 直流电 10
1.5 铝电解车间概况及主要设备 11
1.5.1 铝电解车间概况 11
1.5.2 电解槽排列和母线系统 11
1.5.3 空压站 12
1.5.4 干法净化系统及供料站 12
1.5.5 通风与排烟 12
1.5.6 电力系统 12
1.5.7 车间运输 12
1.5.8 电解厂房主要设备 12
复习思考题 13
2 电解铝生产基本理论知识 14
2.1 铝电解质的组成及其性质 14
2.1.1 铝电解质的组成 14
2.1.2 铝电解质的性质 15
2.2 添加剂对电解质性质的影响 20
2.2.1 氟化铝 20
2.2.2 氟化钙 21
2.2.3 氟化镁 21
2.2.4 氟化锂 22
2.2.5 铝工业电解质的发展 22
2.3 铝电解的两极反应 23
2.3.1 阴极主反应 23
2.3.2 阳极主反应 23
2.3.3 阴阳两极的总反应 23
2.4 铝电解的两极副反应 23
2.4.1 阴极副反应 24
2.4.2 阳极副反应 25
2.5 电解质中氧化铝分解电压 25
复习思考题 26
3 铝电解槽的结构 27
3.1 阴极结构 27
3.1.1 槽壳 27
3.1.2 阴极内衬 28
3.2 上部结构 29
3.2.1 承重桁架 29
3.2.2 阳极提升装置 29
3.2.3 自动打壳下料装置 30
3.2.4 阳极母线和阳极组 31
3.2.5 集气排烟装置 32
3.3 母线结构 32
3.4 电解槽电气绝缘 32
3.4.1 电解槽电气绝缘配置 32
3.4.2 电解系列“零点漂移” 34
复习思考题 36
4 铝电解槽焙烧及启动 37
4.1 铝电解槽焙烧 37
4.1.1 铝液焙烧法 37
4.1.2 焦粒焙烧法 38
4.1.3 石墨粉焙烧法 42
4.1.4 燃料焙烧法 42
4.1.5 四种焙烧法的优缺点比较 43
4.2 铝电解槽启动 45
4.2.1 干法启动 45
4.2.2 湿法启动 46
4.3 电解槽启动后期管理 46
4.3.1 启动初期管理 46
4.3.2 启动后期管理 47
复习思考题 50
5 电解铝正常生产工艺技术条件 51
5.1 电流强度 51
5.2 槽电压 51
5.2.1 槽电压定义 51
5.2.2 槽工作电压 52
5.3 铝水平 54
5.4 电解质水平 54
5.5 电解温度 55
5.6 电解质成分 55
5.6.1 电解质分子比 55
5.6.2 电解质中的氧化铝含量 56
5.6.3 电解质中的添加剂 56
5.7 极距 57
5.8 阳极效应系数 58
5.9 阴极压降 59
5.10 阳极电流密度 59
5.11 覆盖料 59
5.11.1 阳极覆盖料管理的基本原则 59
5.11.2 阳极覆盖料管理的内容 60
5.12 现代铝电解生产管理思路 60
5.12.1 管理遵循标准化、同步化的原则 60
5.12.2 保持平稳的技术条件 60
5.12.3 技术条件比操作质量更重要 61
5.12.4 依靠铝电解控制系统确保人机协调控制 61
5.12.5 重视设备管理 62
5.12.6 运用基于数据分析的决策方法 62
5.12.7 预防为主,处理为辅 63
5.12.8 要注意先天期管理 63
5.12.9 仿生分析思想 63
5.12.10 减少变数(变量)思想 63
复习思考题 64
6 电解铝正常生产工艺操作 65
6.1 下料间隔调整 65
6.1.1 预焙阳极电解槽的定时加料 65
6.1.2 氧化铝下料间隔(NB)的确定 65
6.1.3 下料异常或控制不良的检查与处理 67
6.2 阳极更换 68
6.2.1 确定阳极更换周期 68
6.2.2 确定阳极更换顺序 69
6.2.3 更换阳极的操作步骤 70
6.2.4 异常换极 72
6.3 出铝 72
6.3.1 出铝的基本步骤 72
6.3.2 出铝异常情况的处理 73
6.4 抬母线 74
6.4.1 抬母线周期的估算 74
6.4.2 抬母线作业的基本步骤 74
6.4.3 抬母线异常情况处理 76
6.5 熄灭阳极效应 76
6.5.1 熄灭阳极效应的方法 76
6.5.2 熄灭阳极效应的基本操作步骤 76
6.5.3 熄灭阳极效应作业注意事项 77
6.6 电解质成分调整 77
6.6.1 电解质成分变化经过及原因 77
6.6.2 电解质成分的分析 78
6.6.3 电解质组成的调整 80
6.7 停槽、开槽作业 82
6.7.1 停电停槽作业 82
6.7.2 停电开槽作业 83
6.7.3 不停电停、开槽作业 83
6.8 取电解质试样 86
6.8.1 取样作业准备 86
6.8.2 取样作业实施 86
6.8.3 取样完毕后的处理 87
6.9 电解槽日常维护 87
6.9.1 维护的目的和意图 87
6.9.2 交接班时的巡视 87
6.9.3 正常工作巡视 87
复习思考题 88
7 电解技术参数的测量 89
7.1 铝液高度、电解质高度测定 89
7.1.1 测定位置选择 89
7.1.2 打开测定孔 89
7.1.3 打捞炭渣 89
7.1.4 垂直悬挂测量法 90
7.1.5 侧插测量法 91
7.1.6 测定完毕后的处理 92
7.1.7 注意事项 92
7.2 电解质温度测量 92
7.2.1 测量作业准备 92
7.2.2 测量作业实施 92
7.2.3 测量完毕后的处理 93
7.2.4 注意事项 93
7.3 阳极电流分布测量 93
7.3.1 测量原理与测量工具 93
7.3.2 测量作业准备 94
7.3.3 测量作业实施 94
7.3.4 测量完毕后的处理 94
7.3.5 须终止测量的情况 94
7.4 阳极压降测量 94
7.4.1 测量作业准备 94
7.4.2 测量作业实施 95
7.4.3 测量完毕后的处理 95
7.4.4 须暂停测量的情况 95
7.5 极距测量 95
7.5.1 测量作业准备 96
7.5.2 测量作业实施 96
7.5.3 测量完毕后的处理 96
7.5.4 须终止测量的情况 96
7.6 阴极压降测量 96
7.6.1 测量作业准备 96
7.6.2 测量作业实施 96
7.6.3 测量完毕后的处理 97
7.6.4 须暂停测量的情况 97
7.7 侧部炉帮、伸腿测量作业 97
7.7.1 测量作业准备 97
7.7.2 测量作业实施 98
7.7.3 测量完毕后的处理 99
7.7.4 测量暂停的情况 99
7.8 残极形状测定 99
7.8.1 测定作业准备 99
7.8.2 测定作业实施 99
7.8.3 测定完毕后的处理 100
7.9 炉底隆起测定 100
7.9.1 测定作业准备 100
7.9.2 测定作业实施 100
7.9.3 需重新测定、暂时终止或延期测定的情形 101
7.9.4 测定完毕后的处理 101
7.10 阴极钢棒电流分布测量 102
7.10.1 测量作业准备 102
7.10.2 测量作业实施 102
7.10.3 测量完毕后的处理 102
7.10.4 测量须暂停的情况 102
7.11 阴极钢棒、槽底钢板温度测量 102
7.11.1 测量作业准备 102
7.11.2 阴极钢棒、侧壁温度测量作业的实施 103
7.11.3 槽底钢板温度测量作业的实施 103
7.11.4 测量完毕后的处理 103
7.11.5 测量须终止的情况 103
复习思考题 103
8 电解铝生产异常情况及处理 104
8.1 正常生产槽的特征 104
8.2 电压摆 105
8.2.1 电压摆的定义 105
8.2.2 电压摆的原因 105
8.2.3 电压摆的危害 105
8.2.4 处理电压摆的一般方法 106
8.2.5 处理电压摆的注意事项 107
8.3 冷行程 108
8.3.1 冷行程的定义 108
8.3.2 冷行程的原因 108
8.3.3 冷行程的表现 108
8.3.4 冷行程的危害 108
8.3.5 处理冷行程的一般方法 108
8.3.6 处理冷行程的注意事项 109
8.4 热行程 109
8.4.1 热行程的定义 109
8.4.2 热行程的原因 109
8.4.3 热行程的表现及危害 110
8.4.4 处理热行程的一般方法 111
8.4.5 处理热行程的注意事项 111
8.5 物料平衡的破坏 112
8.5.1 物料不平衡的类型及危害 112
8.5.2 物料不平衡的原因及处理方法 112
8.6 压槽 113
8.7 电解质含炭 114
8.7.1 电解质含炭的定义 114
8.7.2 电解质含炭的危害 114
8.7.3 电解质含炭的表现及原因 114
8.7.4 处理电解质含炭的一般方法及注意事项 115
8.8 滚铝 116
8.8.1 滚铝的原因及危害 116
8.8.2 处理滚铝的一般方法及注意事项 116
8.9 阳极脱落 117
8.9.1 阳极脱落的原因及危害 117
8.9.2 阳极脱落的处理及预防 118
8.10 阳极长包 118
8.10.1 阳极长包的原因 118
8.10.2 处理阳极长包的一般方法 119
8.11 阳极裂纹 119
复习思考题 120
9 电解槽的破损和维护 121
9.1 电解槽的破损 121
9.1.1 电解槽破损的表现 121
9.1.2 电解槽破损的原因 123
9.2 电解槽破损检查与维护 124
9.2.1 电解槽破损的检查与确认 124
9.2.2 破损电解槽的维护 125
9.3 延长电解槽的使用寿命 126
复习思考题 128
10 电解铝生产事故处理及预防 129
10.1 停电 129
10.1.1 电解铝生产对供电系统的要求 129
10.1.2 动力电停电的处置措施 129
10.1.3 直流停电的处置措施 130
10.2 停风 130
10.3 漏炉 131
10.3.1 漏炉的原因和危害 131
10.3.2 漏炉的处置措施 132
10.4 拔槽 132
10.4.1 拔槽的原因和危害 132
10.4.2 拔槽的处置措施 133
10.5 压槽 134
10.5.1 压槽的原因和危害 134
10.5.2 压槽的处置措施 134
10.6 通信中断 134
10.7 难灭效应 135
10.7.1 异常效应的分类 135
10.7.2 难灭效应的原因和危害 135
10.7.3 难灭效应的处置措施 136
10.8 短路口事故 137
复习思考题 138
11 电解槽的计算机控制 139
11.1 计算机控制系统概述 139
11.1.1 计算机控制系统的发展 139
11.1.2 电解铝生产对计算机控制系统的要求 139
11.1.3 计算机控制系统的组成 139
11.2 槽控机概述 140
11.2.1 槽控机的结构 140
11.2.2 槽控机的功能 141
11.2.3 槽控机的操作 142
11.3 铝电解生产控制系统 143
11.3.1 控制系统的控制内容 143
11.3.2 槽电压控制 143
11.3.3 氧化铝浓度控制 144
11.3.4 槽控机的实际应用 145
11.3.5 计算机报表及其分析 149
11.4 数据统计分析系统 150
复习思考题 151
12 电解铝生产主要经济技术指标 152
12.1 产品产量 152
12.2 产品质量 152
12.3 平均电流强度 152
12.4 平均电压 153
12.5 电流效率 153
12.6 铝液氧化铝单耗 154
12.7 铝液氟化盐单耗 154
12.8 铝液阳极毛耗 154
12.9 铝液阳极净耗 154
12.10 铸造损失率 155
12.11 铝液直流电单耗 155
12.12 铝液交流电单耗 155
12.13 电解铝综合交流电耗 156
12.14 提高电流效率的途径 156
12.14.1 铝电解电流效率降低的原因 156
12.14.2 电解生产中提高电流效率的途径 157
12.14.3 几种估算电流效率的方法 161
12.15 降低阳极毛耗的途径 163
12.16 降低平均电压 163
12.17 电解铝的成本 164
12.17.1 电解铝的成本构成 164
12.17.2 降低电解铝成本的途径 165
复习思考题 166
13 氧化铝输送 167
13.1 氧化铝输送原理 167
13.1.1 氧化铝输送分类 167
13.1.2 氧化铝气力输送的压力原理 167
13.1.3 气力输送的流态化原理 169
13.2 氧化铝输送方式 172
13.2.1 稀相输送 172
13.2.2 浓相输送 173
13.2.3 超浓相输送 175
13.2.4 斜溜槽输送 176
13.2.5 其他输送方式 177
13.3 氧化铝输送异常情况及处理 179
13.4 储运、净化安全作业规程 183
复习思考题 184
14 电解烟气净化 185
14.1 电解烟气 185
14.1.1 电解烟气的组成 185
14.1.2 烟气污染物来源 185
14.2 干法净化原理 186
14.2.1 烟气干法净化原理 186
14.2.2 吸附反应 186
14.2.3 净化效率及排放标准 188
14.3 干法净化过程 188
14.3.1 干法净化工艺流程 188
14.3.2 粉尘的过滤 189
14.3.3 清灰 192
14.3.4 除尘器 195
14.3.5 主排烟风机 197
14.3.6 罗茨鼓风机 198
14.4 净化系统异常情况及处理 198
14.5 净化设备安全操作规程 201
14.5.1 主排风机安全操作规程 201
14.5.2 反吹风机安全作业规程 202
14.5.3 罗茨鼓风机安全操作规程 203
14.5.4 高压离心通风机安全操作规程 204
14.5.5 布袋除尘器安全操作规程 205
14.5.6 气力提升机安全操作规程 206
复习思考题 206
15 铝及铝合金熔铸基础知识 207
15.1 铝及铝合金的分类 207
15.1.1 铸造铝合金 207
15.1.2 变形铝合金 209
15.2 铝及铝合金的性质 217
15.2.1 铝的密度 217
15.2.2 熔化温度 217
15.2.3 铝的化学性质 217
15.2.4 铝的流动性 218
15.3 铝及铝合金的性能 218
15.3.1 导电性能 218
15.3.2 力学性能 219
15.3.3 铝的工艺性能 220
15.3.4 铝合金在熔铸过程中的金属烧损 221
15.4 合金元素在铝合金中的作用 221
15.4.1 铜元素 221
15.4.2 硅元素 222
15.4.3 镁元素 222
15.4.4 锰元素 222
15.4.5 锌元素 222
15.5 微量元素与杂质对铝合金性能的影响 223
15.5.1 微量元素的影响 223
15.5.2 杂质元素的影响 224
15.6 变形铝合金制品对锭坯的要求 225
15.6.1 对化学成分的要求 225
15.6.2 对冶金质量的要求 225
15.6.3 对铸锭组织的要求 225
15.6.4 对铸锭几何尺寸和表面质量的要求 226
15.7 铝合金熔铸技术的发展 226
15.7.1 熔铸设备 226
15.7.2 晶粒细化 226
15.7.3 熔体净化和检测 227
15.7.4 铸造技术 228
复习思考题 230
16 铝及铝合金熔炼技术 231
16.1 概述 231
16.1.1 铝合金熔炼的目的 231
16.1.2 铝合金熔炼的特点 231
16.1.3 熔炼炉 232
16.1.4 铝合金熔炼方法 233
16.2 熔炼过程中的物理化学作用 234
16.2.1 炉内气氛 234
16.2.2 液态金属与气体的相互作用 234
16.2.3 影响气体含量的因素 237
16.3 熔炼工艺流程及操作标准 238
16.3.1 普通纯铝的熔炼工艺流程及操作标准 238
16.3.2 铝合金熔炼工艺流程及操作标准 239
16.4 熔炼炉工艺操作标准 240
16.4.1 装炉 240
16.4.2 烘炉 241
16.4.3 洗炉 241
16.4.4 清炉 241
16.4.5 扒渣与搅拌 242
16.4.6 精炼 242
16.4.7 铝锭质量 242
16.5 炉内配料及控制 244
16.5.1 配料的定义 244
16.5.2 配料的作用 245
16.5.3 配料的基本程序 245
16.5.4 配料依据 245
16.5.5 配料计算 245
16.5.6 配料的控制工艺(炉料组成和配比基本原则) 245
16.6 铝液测氢 246
16.7 铝合金熔体净化工艺 247
16.7.1 熔体净化的定义 247
16.7.2 铝及铝合金熔体净化原理 247
16.7.3 熔体净化技术的发展趋势 251
复习思考题 252
17 铝及铝合金铸造技术 253
17.1 铝铸造工艺对铸锭质量的影响 253
17.1.1 铸造温度 253
17.1.2 铸造速度 253
17.1.3 冷却强度 253
17.2 铝锭铸造工艺及设备 254
17.2.1 铝锭铸造机 254
17.2.2 铝锭铸造工艺 255
17.3 圆锭铸造工艺及设备 259
17.3.1 气滑圆锭铸造生产线构成 259
17.3.2 气滑圆锭铸造工艺流程 259
17.4 扁锭铸造生产工艺及设备 261
17.4.1 扁锭铸造生产线构成 261
17.4.2 扁锭铸造工艺流程 261
17.5 电工圆铝杆铸造工艺及设备 264
17.5.1 连铸连轧机生产线构成 264
17.5.2 连铸连轧机工艺 264
17.6 铝母线(铝排)铸造工艺及设备 267
17.6.1 铝母线铸造工艺流程 267
17.6.2 铝母线生产工艺技术条件 267
17.6.3 质量要求 269
17.7 铝及铝合金铸锭均匀化与加工 269
17.7.1 均匀化退火的目的 269
17.7.2 均匀化退火对铸锭组织与性能的影响 269
17.7.3 均匀化退火的温度和时间 269
17.7.4 常见的均匀化要求 270
17.7.5 铸锭机械加工 271
复习思考题 274
18 铝及铝合金铸锭的质量检验及缺陷分析 275
18.1 生产检验 275
18.1.1 生产检验的目的 275
18.1.2 产品质量标准 275
18.2 现场检测技术 276
18.2.1 测氢技术 276
18.2.2 测渣技术 276
18.2.3 板带表面质量检测 276
18.2.4 无损探伤技术 276
18.2.5 化学成分检验 277
18.3 性能检测 277
18.3.1 力学性能检测 277
18.3.2 导电性检测 278
18.4 检测技术发展 279
18.5 重熔用铝锭质量缺陷及控制 279
18.5.1 铝锭的内在质量控制 280
18.5.2 铝锭的内部缺陷控制 282
18.6 圆锭质量缺陷及控制 282
18.6.1 表面缺陷 282
18.6.2 内部缺陷 283
18.7 扁锭质量缺陷及控制 284
18.7.1 凝固时产生的热裂纹的原因及控制措施 284
18.7.2 端面裂缝产生的原因及控制措施 285
18.7.3 拉痕、拉裂原因及控制措施 285
18.7.4 漏铝原因及控制措施 285
18.8 铝母线质量缺陷及影响因素 286
18.8.1 铝母线内部夹渣 286
18.8.2 铝母线气孔 286
18.8.3 中心裂纹、角部裂纹及底部裂纹 286
18.8.4 拉痕或拉裂、表面冷隔 286
18.8.5 水波纹大、弯曲 286
18.8.6 铝母线表面粗糙 287
18.8.7 改进铝母线质量缺陷的措施 287
复习思考题 288
19 筑炉材料 289
19.1 耐火材料的分类、组成和性质 289
19.1.1 耐火材料的分类 289
19.1.2 耐火材料的组成和性质 291
19.2 耐火制品 296
19.2.1 耐火制品的标准牌号、砖号和代号 296
19.2.2 耐火制品的分型定义 297
19.2.3 黏土质耐火制品 298
19.2.4 高铝质耐火制品 299
19.2.5 炭素制品 299
19.2.6 碳化硅耐火制品 300
19.2.7 隔热耐火制品 300
19.2.8 耐火纤维及其制品 300
19.3 隔热耐火材料 301
19.3.1 隔热耐火材料的主要特征 301
19.3.2 隔热材料的分类 301
19.3.3 粉粒状隔热耐火材料 302
19.3.4 纤维状隔热耐火材料 303
19.3.5 复合隔热耐火材料 303
19.4 不定形耐火材料 303
19.4.1 不定形耐火材料的分类 303
19.4.2 耐火浇注料 304
19.4.3 耐火喷射料 304
19.4.4 耐火可塑料 304
19.4.5 耐火捣打料 304
19.4.6 耐火泥浆 304
19.5 耐火材料的应用 305
19.5.1 耐火材料的选用 305
19.5.2 耐火材料在有色冶金中的应用 306
复习思考题 307
20 铝用工业炉的砌筑 308
20.1 砌筑的一般规定及方法 308
20.1.1 耐火砌体的分类 308
20.1.2 工业炉砌筑的允许误差 308
20.1.3 工业炉砌体的砖缝厚度 309
20.1.4 砖的选分和加工 309
20.1.5 炉底砌筑工艺 309
20.1.6 直行炉墙砌筑工艺 311
20.1.7 拐角炉墙砌筑工艺 314
20.1.8 圆形炉墙砌筑工艺 314
20.1.9 拱和顶的砌筑工艺 315
20.2 不定形耐火材料的施工 318
20.2.1 耐火浇注料的施工 318
20.2.2 耐火纤维的施工 320
20.3 铝电解槽 321
20.3.1 铝电解槽内衬结构 321
20.3.2 铝电解槽的砌筑 321
20.4 炭素焙烧炉 324
20.4.1 炭素焙烧炉概况 324
20.4.2 炭素焙烧炉砌筑材料的选用 324
20.4.3 炭素焙烧炉的砌筑(敞开式) 325
20.5 炭素回转窑 327
20.5.1 炭素回转窑概述 327
20.5.2 窑衬的施工 327
20.5.3 沉灰室砌筑 328
20.5.4 冷却机砌筑 329
20.6 铝用混合炉 330
20.6.1 概述 330
20.6.2 施工准备 330
20.6.3 内衬砌筑 330
20.6.4 铝用混合炉的养护 332
20.6.5 烘炉 332
20.7 铝用抬包 332
20.7.1 概述 332
20.7.2 铝用抬包内衬砌筑 332
20.8 铝电解槽内衬砌筑验收规范 333
复习思考题 335
21 筑炉用机械设备 336
21.1 一般规定 336
21.2 筑炉用机械设备 336
21.2.1 搅拌机 336
21.2.2 切砖机 337
21.2.3 手持电动工具 337
21.2.4 卷扬机 338
21.2.5 空气压缩机 338
复习思考题 339
22 电解铝用多功能天车 340
22.1 多功能天车组成机构 340
22.2 多功能天车的液压及气动技术应用 347
22.2.1 液压技术应用 347
22.2.2 气动技术应用 350
22.3 多功能天车的电气设备及其控制 355
22.3.1 多功能天车的电气控制回路 355
22.3.2 多功能天车电气系统的组成 362
22.3.3 多功能天车电气系统的核心部件 363
22.3.4 多功能天车电气系统的电子装置 364
22.4 多功能天车的点检维护保养和安全操作 367
22.4.1 机械部件的点检维护保养 367
22.4.2 电气部件的点检维护保养 368
22.4.3 多功能天车点检、维护、操作的安全操作规程 369
22.5 多功能天车故障及排除方法 374
复习思考题 380
23 电解铝安全生产与环境保护 381
23.1 电解车间安全生产 381
23.1.1 电解车间主要有害因素 381
23.1.2 机械伤害及高处坠落危险 381
23.1.3 铝电解车间安全技术规定 382
23.1.4 铝电解车间一般安全作业规程 382
23.2 铸造车间安全生产 383
23.2.1 铸造车间生产存在的不安全因素 383
23.2.2 铸造车间通用安全管理规定 384
23.2.3 铸造车间天车工安全操作 384
23.2.4 铸造车间天然气安全使用规定 385
23.2.5 铸造车间配料作业安全规定 386
23.2.6 普通铝锭铸造作业安全操作规定 386
23.2.7 圆锭铸造作业安全操作规定 387
23.2.8 连铸连轧铸造作业安全操作规定 387
23.3 筑炉安全生产 388
23.3.1 筑炉作业安全管理规定 388
23.3.2 筑炉施工机械安全使用管理规定 389
23.3.3 脚手架安全使用规定 389
23.3.4 高空作业安全管理规定 390
23.4 环境保护 390
23.4.1 烟气污染物 390
23.4.2 废水治理 391
23.4.3 噪声 392
23.4.4 固体废弃物 393
复习思考题 395
参考文献 396
- 《危险化学品经营单位主要负责人和安全生产管理人员安全培训教材》李隆庭,徐一星主编 2012
- 《绿色过程工程与清洁生产技术 张懿院士论文集精选 上》《绿色过程工程与清洁生产技术》编写组编 2019
- 《润滑剂生产及应用》张远欣,王晓路主编 2012
- 《HSEQ与清洁生产》高峰编著 2019
- 《洗涤剂生产工艺与技术》宋小平,韩长日主编 2019
- 《皮革用化学品生产工艺与技术》宋小平,韩长日著 2018
- 《抗生素生产工艺培训教程》王颖主编 2017
- 《危险化学品生产单位主要负责人及安全生产管理人员培训教材 2018修订版》全国安全生产教育培训教材教材编审委员会 2018
- 《馒头生产技术》刘长虹主编 2019
- 《水泥生产技术与实践》贾华平 2018
- 《市政工程基础》杨岚编著 2009
- 《家畜百宝 猪、牛、羊、鸡的综合利用》山西省商业厅组织技术处编著 1959
- 《《道德经》200句》崇贤书院编著 2018
- 《高级英语阅读与听说教程》刘秀梅编著 2019
- 《计算机网络与通信基础》谢雨飞,田启川编著 2019
- 《看图自学吉他弹唱教程》陈飞编著 2019
- 《法语词汇认知联想记忆法》刘莲编著 2020
- 《培智学校义务教育实验教科书教师教学用书 生活适应 二年级 上》人民教育出版社,课程教材研究所,特殊教育课程教材研究中心编著 2019
- 《国家社科基金项目申报规范 技巧与案例 第3版 2020》文传浩,夏宇编著 2019
- 《流体力学》张扬军,彭杰,诸葛伟林编著 2019
- 《指向核心素养 北京十一学校名师教学设计 英语 七年级 上 配人教版》周志英总主编 2019
- 《北京生态环境保护》《北京环境保护丛书》编委会编著 2018
- 《指向核心素养 北京十一学校名师教学设计 英语 九年级 上 配人教版》周志英总主编 2019
- 《高等院校旅游专业系列教材 旅游企业岗位培训系列教材 新编北京导游英语》杨昆,鄢莉,谭明华 2019
- 《中国十大出版家》王震,贺越明著 1991
- 《近代民营出版机构的英语函授教育 以“商务、中华、开明”函授学校为个案 1915年-1946年版》丁伟 2017
- 《新工业时代 世界级工业家张毓强和他的“新石头记”》秦朔 2019
- 《智能制造高技能人才培养规划丛书 ABB工业机器人虚拟仿真教程》(中国)工控帮教研组 2019
- 《陶瓷工业节能减排技术丛书 陶瓷工业节能减排与污染综合治理》罗民华著 2017
- 《全国职业院校工业机器人技术专业规划教材 工业机器人现场编程》(中国)项万明 2019