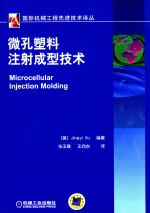
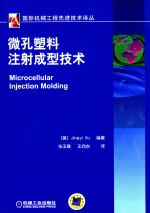
微孔塑料注射成型技术PDF电子书下载
- 电子书积分:14 积分如何计算积分?
- 作 者:(美)徐编著
- 出 版 社:北京:机械工业出版社
- 出版年份:2013
- ISBN:9787111411123
- 页数:422 页
第1章 简介 1
1.1 微孔塑料的发展历史 1
1.2 微孔塑料的优点和应用 3
1.3 与微孔注射成型技术有关的专利和出版物 6
1.4 本书提纲 7
参考文献 7
第2章 微孔注射成型基础理论 9
2.1 微孔注射成型的基本步骤 9
2.2 超临界流体(SCF) 10
2.3 气体在聚合物熔体中的溶解度和扩散能力 12
2.3.1 气体在聚合物熔体中的溶解度 12
2.3.2 气体在聚合物熔体中的扩散速率 28
2.3.3 气体-聚合物混合物的物理性能 30
2.4 泡孔成核 31
2.4.1 成核理论 31
2.4.2 实验得到的成核结果 35
2.5 泡孔长大 41
2.5.1 泡孔长大模型 41
2.5.2 泡孔尺寸分布 44
2.5.3 压力对泡孔尺寸的影响 44
2.5.4 拉伸黏度对泡孔长大的影响 45
2.6 在模具内成型 45
参考文献 45
第3章 微孔材料的形态结构 48
3.1 批处理和注射成型所得试样形态结构的差异 49
3.2 不同材料微孔注塑件的形态结构 51
3.2.1 非结晶性材料 51
3.2.2 结晶性材料 52
3.2.3 共混物和配混材料 54
3.2.4 增强材料和填充材料 55
3.2.5 生物聚合物 58
3.3 泡孔结构表征 59
3.3.1 微孔注射成型注塑件横截面的表层-芯层结构 59
3.3.2 芯层处的泡孔结构 60
3.3.3 界面处的泡孔结构 63
3.3.4 表层处的泡孔结构 63
3.4 泡孔结构对微孔质量的影响 64
3.4.1 泡孔尺寸和密度 64
3.4.2 表层厚度 69
3.4.3 纤维取向 70
3.5 其他特殊泡孔结构 71
3.5.1 超微孔形态结构 71
3.5.2 双峰泡孔结构 71
3.5.3 开孔结构 72
3.5.4 不同气体制备的泡孔结构 73
3.6 结论 73
参考文献 74
第4章 微孔注射成型用材料 76
4.1 聚合物的结构和特征 77
4.1.1 聚合物的种类 77
4.1.2 聚合物的结构 77
4.2 结晶性材料 79
4.2.1 微孔成型用结晶性材料的共性 80
4.2.2 聚丙烯(PP)的微孔成型 81
4.2.3 聚对苯二甲酸丁二酯(PBT)的微孔成型 83
4.2.4 聚对苯二甲酸乙二醇酯(PET)的微孔成型 85
4.2.5 聚酰胺(PA,尼龙)的微孔成型 86
4.2.6 聚甲醛(POM)的微孔成型 86
4.2.7 聚苯硫醚(PPS)的微孔成型 87
4.2.8 其他重要半结晶性材料的微孔成型 88
4.3 非结晶性材料 89
4.3.1 非结晶性材料微孔泡沫的一般性能 90
4.3.2 GPPS的微孔成型 90
4.3.3 PC的微孔成型 90
4.3.4 其他重要非结晶性材料的微孔成型 92
4.4 填料填充的材料 94
4.4.1 有机填料 94
4.4.2 无机填料 95
4.4.3 填料对微孔成型和注塑件性能的影响 96
4.4.4 PP中的成核剂 99
4.4.5 PP中的透明剂 99
4.5 纤维增强材料 100
4.5.1 有机纤维 100
4.5.2 无机纤维 101
4.6 纳米材料增强复合材料 102
4.6.1 纳米粘土填充的PE-HD 103
4.6.2 纳米粘土填充的PA6 103
4.6.3 纳米粘土填充的PP 104
4.6.4 纳米粘土填充的GPPS 104
4.6.5 纳米粘土填充的PE-LD 104
4.6.6 纳米粘土填充的PBT 105
4.7 共混物和配混材料 105
4.7.1 Nory1?的微孔成型 106
4.7.2 丙烯腈-丁二烯-苯乙烯(ABS)的微孔成型 108
4.7.3 PC/ABS合金 109
4.7.4 PC/PBT合金 110
4.7.5 交联EVAC的微孔成型 111
4.7.6 Kraton G-7722的微孔成型 111
4.7.7 不相容共混物的微孔成型 111
4.8 金属粉末 112
4.9 生物聚合物 113
4.9.1 加工参数对PCL可发泡性的影响 115
4.9.2 发泡剂对PCL可发泡性的影响 115
4.9.3 分子结构改性对PLA可发泡性的影响 116
4.9.4 填料对PLA可发泡性的影响 116
4.9.5 植物蛋白质泡沫 116
4.9.6 生物聚合物共混物 117
参考文献 117
第5章 微孔注射成型设计 120
5.1 注塑件设计 120
5.1.1 注塑件几何形状设计 120
5.1.2 注塑件的性能 126
5.1.3 微孔注塑件的组装 137
5.2 模具设计 137
5.2.1 模具材料 137
5.2.2 模具表面涂覆和结构化 139
5.2.3 模具排气 141
5.2.4 模具分流道和浇口 143
5.2.5 模具冷却系统 148
5.2.6 模具推出系统 149
5.3 材料性能与减重幅度 150
5.3.1 拉伸强度模型 151
5.3.2 弯曲强度模型 153
5.3.3 Izod冲击强度模型 153
5.3.4 拉伸强度模型应用结果 154
5.3.5 弯曲强度模型应用结果 156
5.3.6 冲击强度模型应用结果 157
5.3.7 微孔注塑件力学性能的提高 157
5.3.8 力学性能建模和改进方法的有关结论 159
5.4 通过模具设计和注塑件设计提高表面质量 159
5.4.1 材料 160
5.4.2 通过注塑件设计解决表面质量问题 160
5.4.3 通过模具设计解决表面质量问题 161
参考文献 162
第6章 微孔泡沫注射成型工艺 164
6.1 气体计量 164
6.1.1 微孔泡沫用螺杆的塑化量 164
6.1.2 气体计量量 167
6.1.3 气体计量压力设定 173
6.1.4 气体计量时间 175
6.1.5 气体计量结论 175
6.2 气体混合和扩散 176
6.2.1 混合的影响 176
6.2.2 温度的影响 179
6.2.3 压力的影响 180
6.2.4 停留时间的影响 181
6.2.5 材料的影响 182
6.2.6 微孔成型第一阶段的实验结果 183
6.2.7 对空注射并确定单相溶液的质量 190
6.2.8 有关气体混合和分散的结论 193
6.3 成核和初始泡孔长大 193
6.3.1 注射过程中的成核理论 193
6.3.2 温度的影响 194
6.3.3 压力降速率的影响 194
6.3.4 注射速度的影响 197
6.3.5 成核位置的影响 198
6.3.6 材料的影响 198
6.3.7 气体用量的影响 200
6.4 充模分析 201
6.4.1 注射速度 202
6.4.2 注射速度曲线 205
6.4.3 模具温度 207
6.4.4 收缩和翘曲 208
6.4.5 脱模 208
6.4.6 通过加工来提高表面质量 208
6.4.7 优化微孔注射成型工艺 213
6.4.8 模具温度对微孔注射成型的影响 215
6.4.9 湿度对微孔注射成型的影响 216
6.4.10 微孔注射成型时熔体温度的影响 218
6.4.11 微孔注射成型过程中出现的问题及其解决方案 218
6.5 微孔注射成型与气体辅助注射成型的比较 220
6.5.1 气体和熔体相 220
6.5.2 气体压力 220
6.5.3 模具设计 221
6.5.4 模具冷却 221
6.6 微孔注射成型与结构发泡成型的比较 222
6.6.1 厚度和泡孔尺寸 222
6.6.2 第一阶段的压力 222
6.6.3 性能变化 222
6.6.4 设备 222
6.7 微孔注射成型与传统注射成型的比较 222
6.7.1 保压阶段 222
6.7.2 压力 222
6.7.3 冷却 223
6.7.4 脱模 223
6.7.5 设备 223
6.7.6 成型周期 223
6.8 微孔注射成型与微孔挤出成型的比较 224
6.8.1 连续过程(挤出成型)与非连续过程(注射成型)的比较 224
6.8.2 螺杆设计和性能 224
6.8.3 成核 224
6.8.4 定型过程 224
6.8.5 物料 225
6.8.6 压力 225
6.9 微孔注射成型与微孔中空成型的比较 225
6.9.1 连续型坯挤出 225
6.9.2 中间过渡型坯工艺 226
参考文献 226
第7章 微孔注射成型装置 228
7.1 微孔注射成型的两个阶段 228
7.2 往复式螺杆注射成型机 229
7.2.1 单向阀和阀浇口 230
7.2.2 微孔注射成型用螺杆和机筒 236
7.2.3 微孔注射螺杆头 252
7.2.4 锁紧装置 257
7.2.5 微孔注射成型装置的结构及参数 260
7.2.6 微孔注射成型的液压系统 266
7.2.7 微孔注射成型的控制系统 272
7.2.8 美国塑料工业协会气体计量过程的指导原则 273
7.3 挤出机与注射成型机的结合 274
7.3.1 挤出机上的SCF计量装置 275
7.3.2 注射柱塞装置 275
7.3.3 保持挤出机内压力的方法 275
7.3.4 螺杆-柱塞式注射成型机的发展 276
7.4 SCF输送系统设计 276
7.4.1 物理发泡剂 277
7.4.2 泵对发泡剂加压 277
7.4.3 气体注射器设计 278
7.4.4 气体计量控制系统 280
7.4.5 气体调节器 281
7.4.6 气体输送系统的安全 281
7.5 气体计量用的烧结金属环(Optifoam?) 282
7.6 气体计量用的动态混合器(Ergocell?) 283
7.7 气体计量时在密封的料斗中加气(ProFoam?) 283
7.8 微孔成型的设备改造 283
7.9 液体硅橡胶的气体计量混合器 284
7.10 微孔注射成型的配套装置 284
参考文献 285
第8章 特殊工艺 287
8.1 共注射(夹芯)成型微孔注塑件 287
8.1.1 微孔共注射成型的充模分析 287
8.1.2 微孔共注射用材料 292
8.1.3 微孔共注射方法 292
8.1.4 微孔共注塑件和模具设计 294
8.1.5 微孔共注射成型结论 301
8.2 气体反压注射成型 302
8.2.1 气体反压注射成型工艺 302
8.2.2 模具和注塑件设计 304
8.2.3 气体反压模具的气体控制系统 305
8.2.4 气体反压注射成型微孔注塑件的结构和物理性能 306
8.3 叠塑 308
8.4 反向铸压 310
8.5 叠塑与反向铸压共用工艺 312
8.6 冷热模具工艺 313
8.7 不减重的超微孔结构 314
8.8 发泡最轻时的最低气体用量 315
8.9 微孔泡沫中所用的化学发泡剂 315
8.9.1 产生N2的化学发泡剂 316
8.9.2 产生CO2的化学发泡剂 316
8.9.3 化学发泡剂改善熔体充模流动性能及缩短冷却时间 316
8.9.4 使用化学发泡剂时的设计建议 317
8.9.5 使用化学发泡剂时的加工建议 317
8.9.6 吸热/放热混合型发泡剂 318
8.9.7 化学发泡剂成型时出现的问题及其解决方案 318
8.9.8 化学发泡剂方面未来的工作 319
8.10 水作发泡剂 320
8.11 应力发泡 321
8.12 微孔金属注塑件 322
8.13 局部微孔泡沫 324
8.14 薄壁微孔泡沫 325
参考文献 327
第9章 微孔注射成型的模拟 329
9.1 裹气材料的流变性能数据和pVT数据 329
9.1.1 超临界流体和塑料熔体混合物的流变性能 330
9.1.2 超临界流体和塑料熔体混合物的pVT数据库 338
9.2 微孔注射成型的Moldflow模拟 339
9.2.1 理论 340
9.2.2 实验与模拟 344
9.3 微孔注射成型的简单模拟 357
9.3.1 黏度模型 358
9.3.2 气体溶解度和浓度的计算 361
9.3.3 气体扩散的计算 361
9.3.4 泡孔长大的计算 362
9.4 MuCell?工艺充模模拟的指导原则 363
参考文献 364
第10章 微孔注射成型注塑件的后加工与性能测试 366
10.1 微孔注塑件的焊接 366
10.1.1 技术原理 367
10.1.2 焊接方法 367
10.1.3 PA6和PA66的实验结果 370
10.1.4 超声波焊接其他材料的实验结果 375
10.2 表面抛光和喷涂 376
10.2.1 表面抛光 376
10.2.2 喷涂 376
10.3 后冷却 377
10.4 脱气过程 377
10.5 微孔注塑件的性能测试 377
10.5.1 冲击性能测试 378
10.5.2 拉伸性能测试 378
10.5.3 弯曲性能测试 378
10.5.4 动态力学性能分析 378
10.5.5 低剪切流变性能测试 378
10.5.6 热性能测试 378
10.5.7 收缩率测试 378
10.5.8 燃烧性能测试 378
10.5.9 声学性能测试 379
10.5.10 密度测试 379
参考文献 379
第11章 微孔注射成型制品的市场与应用 380
11.1 微孔注射成型制品的市场分析 380
11.1.1 低成本产品 380
11.1.2 高质量产品 381
11.1.3 微孔结构的独特性能 382
11.1.4 绿色产品 382
11.1.5 其他 382
11.2 典型应用案例研究 383
11.2.1 薄壁注塑件 383
11.2.2 汽车件 385
11.2.3 五金件 391
11.2.4 电气部件 392
11.2.5 精密成型件 394
11.2.6 医疗器件 394
11.2.7 金属和陶瓷粉末注塑件 395
11.2.8 高性能工程材料 395
11.2.9 特殊微孔结构 395
11.2.10 微孔发泡瓶 395
11.3 未来的研究课题及潜在应用 396
11.3.1 超微孔注塑件 396
11.3.2 特殊功能注塑件 396
11.3.3 采用超临界流体的特殊加工 397
参考文献 398
第12章 微孔注射成型的成本节省 399
12.1 材料节省 400
12.1.1 基材 400
12.1.2 发泡剂 401
12.1.3 添加剂 401
12.2 模具 402
12.3 设备 403
12.4 成型过程 406
12.4.1 冷却过程 406
12.4.2 保压 407
12.4.3 注射时间 407
12.4.4 螺杆回位时间 407
12.4.5 脱模时间 407
12.4.6 特殊微孔加工技术——海豚皮技术 408
12.4.7 薄壁成型的微小泡孔 408
12.4.8 低黏度熔体 408
12.4.9 其他 408
12.4.10 成型周期缩短的经验总结 408
12.5 尺寸稳定性 409
12.5.1 保持尺寸公差的夹具 409
12.5.2 后热处理 409
12.5.3 后机械加工 409
12.5.4 根据组装尺寸分组 409
12.6 微孔泡沫的性能提高 410
12.6.1 隔热性能 410
12.6.2 减振性能 410
12.6.3 隔声性能 410
12.6.4 质轻 410
12.6.5 无应力注塑件 410
12.6.6 通过将不同材料组合实现特定性能 411
12.6.7 可回收的废旧材料 411
12.7 投资回报分析(ROI) 411
12.8 不同成型工艺的成本比较 411
12.9 节能案例分析 412
参考文献 416
附录 417
附录A 压力降速率dp/dt公式(第7章) 417
附录B 模板变形量相同时锁紧载荷W与支撑距离L间的关系(第7章) 418
附录C 发泡与未发泡注塑件的拉伸强度比(第5章) 418
附录D 实际减重比的计算(第5章) 419
附录E 发泡与未发泡注塑件的弯曲强度比(第5章) 420
附录F vm与vt之间的关系(第6章) 420
附录G 喷嘴型流变仪环形槽黏度模型(第9章) 421
- 《现代药物制剂新技术丛书 预灌封注射剂技术与应用》马贤鹏编 2017
- 《塑料成型工艺与模具设计》王春艳 2018
- 《塑料模具CAE技术及应用》陈开源主编 2019
- 《陶瓷拉坯成型法》(美)本·卡特(BenCarter)著 2019
- 《塑料海洋》(美)查尔斯·穆尔(CharlesMoore),(美)卡桑德拉·菲利普斯(CassandraPhillips)著 2019
- 《机械工程材料与成型技术》(中国)刘贯军 2019
- 《面部精准注射解剖图谱》隋鸿锦,郝立君,于胜波主编;淳璞,李菲菲,王琳,徐海倩,李哲等副主编 2019
- 《塑料助剂与配方设计》左建东,罗超云,王文广主编 2018
- 《塑料门窗和PVC-U异型材生产技术与经营、管理、营销知识》杨忠久主编 2017
- 《注射无小事》莫永珍,万静波主编 2016
- 《指向核心素养 北京十一学校名师教学设计 英语 七年级 上 配人教版》周志英总主编 2019
- 《北京生态环境保护》《北京环境保护丛书》编委会编著 2018
- 《高等教育双机械基础课程系列教材 高等学校教材 机械设计课程设计手册 第5版》吴宗泽,罗圣国,高志,李威 2018
- 《指向核心素养 北京十一学校名师教学设计 英语 九年级 上 配人教版》周志英总主编 2019
- 《高等院校旅游专业系列教材 旅游企业岗位培训系列教材 新编北京导游英语》杨昆,鄢莉,谭明华 2019
- 《中国十大出版家》王震,贺越明著 1991
- 《近代民营出版机构的英语函授教育 以“商务、中华、开明”函授学校为个案 1915年-1946年版》丁伟 2017
- 《新工业时代 世界级工业家张毓强和他的“新石头记”》秦朔 2019
- 《智能制造高技能人才培养规划丛书 ABB工业机器人虚拟仿真教程》(中国)工控帮教研组 2019
- 《AutoCAD机械设计实例精解 2019中文版》北京兆迪科技有限公司编著 2019