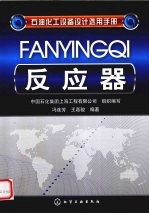
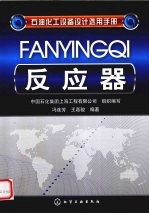
反应器PDF电子书下载
- 电子书积分:9 积分如何计算积分?
- 作 者:中国石化集团上海工程有限公司编写
- 出 版 社:北京:化学工业出版社
- 出版年份:2010
- ISBN:9787122074195
- 页数:195 页
第1章 化学反应器设计原理 1
1.1 化学反应器概述 1
1.1.1 化学反应器形式 1
1.1.2 化学反应器应用 2
1.2 化学反应器工艺设计 2
1.2.1 停留时间分布 2
1.2.1.1 停留时间的定义与表征 2
1.2.1.2 RTD对反应过程的影响 4
1.2.2 宏观混合与微观混合 4
1.2.3 反应器形式对聚合反应过程的影响 5
1.2.3.1 聚合反应的特点 5
1.2.3.2 返混对聚合物分子量分布的影响 6
1.2.3.3 微观混合对聚合物分子量分布的影响 7
1.3 化学反应器放大 8
1.3.1 放大技术概述 8
1.3.2 几何相似放大 8
1.3.2.1 几何相似放大法概要 8
1.3.2.2 不同搅拌目的时的放大准则 9
1.3.2.3 采用不同的放大准则时,混合参数的变化规律 11
1.3.2.4 采用不同放大准则时,传热系数的变化规律 12
1.3.2.5 由实验确定几何相似放大准则 13
1.3.3 非几何相似放大 14
1.3.4 实例——氯乙烯悬浮聚合反应器放大 14
第2章 低黏搅拌反应器 17
2.1 搅拌设备概述 17
2.1.1 引言 17
2.1.2 搅拌技术的研究进展 17
2.1.3 新型高效节能搅拌设备的研发 17
2.1.4 测量技术的进展 18
2.1.5 模拟仿真技术 19
2.2 功率特性 20
2.2.1 搅拌功率概述 20
2.2.2 永田进治的搅拌功率计算式 20
2.2.2.1 无挡板时的搅拌功率 21
2.2.2.2 有挡板时的搅拌功率 21
2.2.2.3 圆管的挡板系数 22
2.2.3 布鲁马金式叶轮的功耗和排量 22
2.2.4 三叶后掠叶轮的功耗和排量 23
2.3 循环特性 24
2.4 混合速率 25
2.5 搅拌选型与设计 28
2.5.1 搅拌设备设计的过程因素 28
2.5.2 搅拌设备选型、设计和优化步骤 30
2.5.3 搅拌设计范围 32
2.5.4 设计步骤 32
2.5.5 过程因素分析 33
2.5.6 实例——乳液聚合 34
2.6 CFD技术应用 37
2.7 实例——搅拌器混合计算 37
2.7.1 实验装置与测量方法 37
2.7.2 CFD模拟方法 38
2.7.3 结果与讨论 39
2.7.3.1 混合时间的数值模拟与实验对比 39
2.7.3.2 混合过程的数值模拟与实验对比 40
2.7.4 结论 41
第3章 高黏搅拌反应器 43
3.1 高黏性体系的搅拌功率 43
3.2 立式高黏搅拌 44
3.2.1 锚式叶轮 44
3.2.2 框和偏框式叶轮 46
3.2.3 双螺带式和单螺带式叶轮 47
3.2.4 内外单螺带式与螺带螺杆式叶轮 48
3.2.5 求解ks方法的比较 52
3.2.6 螺杆-导流筒式叶轮 53
3.3 实例——顺丁橡胶反应器 54
3.3.1 工业装置尺寸 54
3.3.2 流变数据 54
3.3.3 内外单螺带桨功耗计算实例 55
第4章 脱挥反应器 57
4.1 概论 57
4.2 相际传质与脱挥原理 57
4.2.1 脱挥理论 57
4.2.2 传质过程系数模型 58
4.2.2.1 脱挥的一般扩散传质模型 58
4.2.2.2 停留时间分布——渗透传质溶合数学模型 59
4.2.3 高黏流体脱挥及强化方法 59
4.2.3.1 加入第二流体的方法——热力学强化手段 59
4.2.3.2 多级脱挥 60
4.2.3.3 强化传质面的表面更新速率 60
4.3 高黏流体脱挥器 60
4.3.1 落条式脱挥器 60
4.3.2 立式搅拌成膜脱挥器 60
4.3.3 卧式表面更新脱挥器 61
4.3.4 螺杆挤出机 61
4.4 自清洁反应器在高黏流体脱挥中的应用 62
4.4.1 自清洁反应器的特点 62
4.4.2 高黏自清洁反应器研究进展 62
4.4.3 排气式挤出机 63
4.4.3.1 自清洁式SCR和新型SCR双螺杆挤出机 64
4.4.3.2 BIVOLAV双螺杆挤出机 64
4.4.4 实例——LIST-ORP和LIST-CRP 65
4.4.4.1 工作原理 66
4.4.4.2 设备尺寸与配置 67
4.5 本章小结 68
第5章 气液相反应器 69
5.1 气液相反应概述 69
5.2 气液相测量方法 70
5.2.1 平均参数的测量 70
5.2.1.1 测压法 70
5.2.1.2 衰减法 71
5.2.1.3 床层塌落法 71
5.2.1.4 液位差法 71
5.2.1.5 溢流法 73
5.2.2 局部参数的测量 73
5.3 搅拌槽内气泡尺寸的实验研究 73
5.3.1 搅拌器对搅拌槽内平均气泡大小分布的影响 73
5.3.2 搅拌转速对气泡尺寸变化的影响 74
5.3.3 气体分布器、挡板对气泡尺寸的影响 75
5.3.4 通气对气泡尺寸变化的影响 76
5.3.5 物性对气泡尺寸变化的影响 76
5.3.5.1 电介质的影响 76
5.3.5.2 黏度的影响 77
5.3.5.3 固体颗粒的影响 77
5.3.5.4 温度和压力的影响 78
5.3.6 气泡尺寸预测与数据关联 78
5.3.6.1 最大气泡尺寸dmax的理论预测 78
5.3.6.2 气泡尺寸的数据关联 78
5.4 搅拌槽内气含率的实验研究 80
5.4.1 搅拌槽内局部气含率 80
5.4.2 搅拌槽内平均气含率的实验研究 80
5.4.3 平均气含率关联式 81
5.5 通气功率特性 82
5.5.1 组合桨对功率特性的影响 82
5.5.2 通气对搅拌功率的影响 83
5.5.3 桨间距及底层桨离底距离对搅拌功率的影响 84
5.5.4 通气搅拌功率的数据关联式 84
5.6 新型搅拌器开发与桨组合优化 85
5.6.1 新型搅拌器开发 85
5.6.2 搅拌桨优化组合 86
5.7 搅拌反应器内气液两相流CFD模拟研究 87
5.7.1 双流体模型 87
5.7.1.1 基本控制方程 87
5.7.1.2 动量传输 88
5.7.2 气相和液相湍动模型 90
5.7.3 气液搅拌槽中的两相流模拟实践 91
5.7.3.1 单一气泡尺寸的气液两相流的CFD研究 91
5.7.3.2 基于PBM模型的气液两相流的CFD研究 92
5.7.3.3 One-group PBM模型 92
5.7.3.4 Multi-group PBM模型 93
5.7.3.5 基于PBM的气液两相流的CFD研究 96
5.8 实例——PX氧化反应器 97
5.8.1 功率计算 97
5.8.1.1 启动功率估算 97
5.8.1.2 正常操作时功率估算 97
5.8.2 工业组合桨气含率 99
5.8.2.1 层间距的影响 99
5.8.2.2 分布器类型的影响 100
5.8.2.3 槽径的影响 100
5.8.3 工业组合桨的传质特性 101
5.8.3.1 气液传质系数 101
5.8.3.2 操作特性 102
5.8.3.3 搅拌转速的影响 102
5.8.3.4 分布器的影响 103
5.8.3.5 桨径的影响 104
5.8.3.6 小结 104
5.8.4 PX氧化反应器(30万吨/年)工业装置核算 105
5.8.4.1 功率 105
5.8.4.2 气含率 106
5.8.4.3 临界转速 106
第6章 固液相反应器 109
6.1 固液悬浮概述 109
6.2 固液悬浮判据 109
6.2.1 以槽底未悬浮固体量作判据 110
6.2.2 以槽内悬浮液的均匀程度作判据 110
6.2.3 完全离底的临界转速 110
6.3 固液悬浮搅拌设备 112
6.3.1 搅拌器 112
6.3.2 桨径与槽径之比 115
6.3.3 槽底形状 115
6.4 物性对固液悬浮的影响 116
6.4.1 液相黏度的影响 116
6.4.2 固相分率φv的影响 117
6.4.3 粒子大小的影响 117
6.5 固液悬浮搅拌槽的放大 117
6.6 自浮颗粒的悬浮分散 118
6.6.1 分散状态 119
6.6.2 挡板的影响 120
6.6.3 桨型的影响 121
6.6.4 放大规则 122
6.6.5 旋涡深度 123
6.7 实例——顺丁橡胶溶液的凝聚过程 123
6.7.1 凝聚机理 123
6.7.2 凝聚釜 124
6.7.3 “闷釜”现象分析 125
6.8 气固液三相悬浮分散 125
6.8.1 固体临界悬浮转速 126
6.8.2 搅拌功耗 127
6.8.3 气含率和传质 129
6.8.4 釜型和挡板的影响 129
6.8.5 桨型和桨间距的影响 130
6.8.6 气体分布器的影响 132
6.8.7 颗粒物性等的影响 133
6.8.8 混合时间 134
6.8.9 放大规则 134
6.8.10 表面活性剂的影响 135
6.9 实例——Hypol液气本体法丙烯聚合过程 135
6.9.1 过程简介 135
6.9.2 过程分析 135
第7章 流态化反应器 137
7.1 气固流态化概述 137
7.1.1 颗粒的分类 137
7.1.2 流化状态的判别 138
7.1.3 最小流化速度 140
7.1.4 最小鼓泡速度 141
7.1.5 流化床中的流动特性 142
7.2 流化床中的检测技术 143
7.2.1 颗粒性质的测量方法 143
7.2.2 流体力学特性的测量 143
7.2.3 颗粒浓度的测量 144
7.2.4 颗粒速度的测量 145
7.2.5 压力信号 145
7.3 气固稀相流化床 146
7.3.1 循环流化床反应器 146
7.3.2 MZCR反应器 147
7.3.3 提升管中气固两相流动行为 148
7.4 搅拌流化床 149
7.5 计算流体力学在气固流化床的应用 150
7.5.1 双流体模型 151
7.5.2 随机颗粒轨道模型 151
7.5.3 离散元模型 152
7.6 实例——聚酯切片流化床反应器 152
7.6.1 流化状态的变化 153
7.6.2 床层膨胀比 153
7.6.3 床层压降 154
7.6.4 压力脉动与功率谱分析 154
7.6.5 Froude数的分析 155
7.6.6 能量分析 156
7.6.7 小结 157
7.7 展望 157
第8章 管式反应器 159
8.1 静态混合反应器 159
8.1.1 静态混合器 159
8.1.1.1 旋扭叶片型静态混合器 159
8.1.1.2 波纹片、窄板条型静态混合器 163
8.1.1.3 其他类型静态混合器 165
8.1.2 新型静态混合器的开发 165
8.2 移动管式反应器 167
8.2.1 液固循环移动床反应器 167
8.2.2 液固环流反应器 168
8.2.3 液固提升管-流化床反应器 171
8.2.4 高黏度固液非均相高效反应器 173
8.2.5 环管反应器 175
8.2.6 液固二相光催化剂反应器 175
8.2.7 液固下喷自吸环流反应器 176
8.3 小结 177
符号说明 178
参考文献 183
- 《市政工程基础》杨岚编著 2009
- 《工程静力学》王科盛主编 2019
- 《中央财政支持提升专业服务产业发展能力项目水利工程专业课程建设成果 设施农业工程技术》赵英编 2018
- 《化学反应工程》许志美主编 2019
- 《绿色过程工程与清洁生产技术 张懿院士论文集精选 上》《绿色过程工程与清洁生产技术》编写组编 2019
- 《软件工程》齐治昌,谭庆平,宁洪编著 2019
- 《化学工程与工艺专业实验指导》郭跃萍主编 2019
- 《药物合成反应》姚其正主编 2019
- 《天水师范学院60周年校庆文库 新工科视域下的工程基础与应用研究》《天水师范学院60周年校庆文库》编委会编 2019
- 《高等工程教育改革探析》李瀛心,吴价宝著 1997
- 《东方杂志 第110册 第25卷 第一至四号 1928年1月-1928年2月》上海书店出版社编 2012
- 《国学经典诵读》(中国)严琼燕 2019
- 《现代水泥技术发展与应用论文集》天津水泥工业设计研究院有限公司编 2019
- 《思维导图 超好用英语单词书》(中国)王若琳 2019
- 《东北民歌文化研究及艺术探析》(中国)杨清波 2019
- 《中国当代乡土小说文库 本乡本土》(中国)刘玉堂 2019
- 《两京烟云》陈诗泳,赖秀俞责任编辑;(中国)千慧 2019
- 《HTML5从入门到精通 第3版》(中国)明日科技 2019
- 《MBA大师.2020年MBAMPAMPAcc管理类联考专用辅导教材 数学考点精讲》(中国)董璞 2019
- 《莼江曲谱 2 中国昆曲博物馆藏稀见昆剧手抄曲谱汇编之一》郭腊梅主编;孙伊婷副主编;孙文明,孙伊婷编委;中国昆曲博物馆编 2018