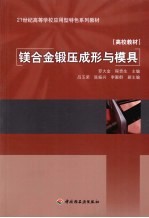
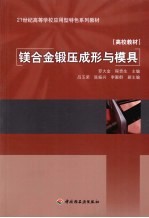
镁合金锻压成形与模具PDF电子书下载
- 电子书积分:12 积分如何计算积分?
- 作 者:罗大金编著
- 出 版 社:北京:中国轻工业出版社
- 出版年份:2010
- ISBN:9787501973750
- 页数:320 页
第1章 变形镁合金概述 1
1.1 变形镁合金的发展现状 1
1.1.1 概述 1
1.1.2 变形镁合金的应用 2
1.2 变形镁合金的牌号和分类 4
1.2.1 变形镁合金的牌号 4
1.2.2 变形镁合金的分类 5
1.3 镁合金固态成形的理论基础 7
1.3.1 固态成形的基本概念 7
1.3.2 固态成形的力学基础 9
1.3.3 镁合金固态成形的特点 12
1.4 镁合金固态成形技术 14
1.4.1 锻造 14
1.4.2 挤压 14
1.4.3 冲压 14
1.4.4 轧制 15
第2章 镁合金模锻工艺 17
2.1 镁合金的可锻性 17
2.2 镁合金的锻造方式 17
2.2.1 自由锻造 17
2.2.2 模型锻造 17
2.2.3 等温锻造与等温精锻 18
2.3 镁合金锻造工艺 20
2.3.1 锻造的主要工序 20
2.3.2 锻件的热处理 23
2.3.3 镁合金锻后的性能变化 24
2.3.4 镁合金锻件缺陷及其防止措施 24
2.4 锻模设计基础 25
2.4.1 锻模分类 25
2.4.2 模膛及模锻工步分类 26
2.5 模锻设备 28
2.5.1 锻锤 28
2.5.2 热模锻压力机 30
2.5.3 螺旋压力机 32
2.5.4 平锻机 33
第3章 锻模设计 36
3.1 锤上模锻锻模设计 36
3.1.1 锤上模锻的特点 36
3.1.2 锻件图的设计 37
3.1.3 锤上模锻工步选择 46
3.1.4 终锻模膛的设计 54
3.1.5 预锻模膛的设计 57
3.1.6 制坯模膛设计 62
3.2 热模锻压力机锻模设计 67
3.2.1 锻件图特点 67
3.2.2 模膛的设计 68
3.3 平锻机上锻模设计 72
3.3.1 锻件图设计特点 72
3.3.2 模锻工步的确定 74
3.4 摩擦压力机模锻设计 77
3.4.1 锻件图设计特点 77
3.4.2 锻模设计特点 78
第4章 冲裁工艺与冲模设计 81
4.1 冲裁变形过程分析 81
4.1.1 冲裁变形过程 81
4.1.2 冲裁变形力曲线 82
4.1.3 冲裁零件断面形状 82
4.2 冲裁件质量分析 82
4.2.1 间隙对切断面质量的影响 83
4.2.2 间隙对尺寸精度的影响 83
4.2.3 刃口状态对断面质量的影响 85
4.3 凸、凹模间隙值的确定 86
4.3.1 间隙对冲裁过程的影响 86
4.3.2 间隙值的确定 86
4.4 凸、凹模刃口尺寸计算 91
4.4.1 尺寸计算原则 91
4.4.2 尺寸计算方法 92
4.5 冲裁力的计算 96
4.5.1 冲裁变形力 96
4.5.2 卸料力及推件力 98
4.5.3 冲裁时的总压力 99
4.6 冲裁件的排样 100
4.6.1 排样目的 100
4.6.2 排样方法 100
4.6.3 排样工艺参数 101
4.6.4 条料宽度的计算 102
4.6.5 条料在板料上的排样 105
4.6.6 材料的利用率 106
4.7 冲裁模的分类及结构分析 106
4.7.1 冲裁模的分类 106
4.7.2 冲裁模的结构分析 107
4.7.3 冲裁模设计的一般程序 114
4.7.4 冲裁模的总体设计 121
第5章 弯曲工艺与弯曲模具设计 126
5.1 弯曲变形过程分析 126
5.1.1 弯曲变形过程 126
5.1.2 弯曲的应力应变 127
5.2 弯曲件的回弹及减少回弹的方法 129
5.2.1 影响回弹的因素 129
5.2.2 回弹值的确定 130
5.2.3 减少回弹的措施 131
5.3 最小弯曲半径 133
5.3.1 含义和作用 133
5.3.2 最小弯曲半径的确定 133
5.3.3 影响最小弯曲半径的因素 134
5.4 弯曲件毛坯尺寸的计算 135
5.4.1 变形中性层位置的确定 135
5.4.2 弯曲件毛坯尺寸的计算 136
5.5 弯曲力的计算 138
5.6 弯曲件的工序安排及模具设计 140
5.6.1 常见弯曲件的工序安排 140
5.6.2 V形件的弯曲 140
5.6.3 U形件的弯曲 142
5.6.4 帽罩形件的弯曲 142
5.6.5 Z形件的弯曲 144
5.6.6 圆筒形件的弯曲 144
5.6.7 其他形状的弯曲件 145
5.7 弯曲模工作部分尺寸设计 146
5.7.1 凸、凹模的圆角半径及弯曲凹模的深度 146
5.7.2 凸、凹模间隙 147
5.7.3 凸、凹模工作部分的尺寸与公差 148
第6章 拉延工艺及模具设计 150
6.1 拉延变形过程分析 150
6.1.1 拉延变形过程 150
6.1.2 拉延过程中毛坯的应力与应变状态 152
6.2 圆筒形件的拉延 154
6.2.1 毛坯尺寸的计算 154
6.2.2 拉延系数和拉延次数 155
6.2.3 以后各次拉延的特点 161
6.2.4 以后各次拉延的方法 161
6.2.5 压边力、拉延力和拉延功的计算 162
6.2.6 凸、凹模工作部分设计 167
6.3 带凸缘筒形件的拉延 172
6.3.1 小凸缘件的拉延 172
6.3.2 宽凸缘件的拉延 172
6.4 矩形件的拉延 175
6.4.1 矩形件拉延的特点 175
6.4.2 毛坯计算方法 176
6.4.3 高矩形件拉延工艺过程 180
6.4.4 模具间隙、圆角半径的确定 182
6.5 拉延工作中的润滑、退火与酸洗 183
6.5.1 润滑 183
6.5.2 退火 184
6.5.3 中间退火 184
6.5.4 酸洗 186
6.6 拉深模具的分类及典型结构 187
6.6.1 首次拉深模 187
6.6.2 后续各工序拉延模 188
6.7 拉延件的废品种类、产生原因及预防方法 189
第7章 其他成形方法及模具 191
7.1 局部成形和翻边 191
7.1.1 局部成形 192
7.1.2 翻边 193
7.2 缩口和胀形 199
7.2.1 缩口 200
7.2.2 胀形 202
7.3 校平和整形 204
7.3.1 校平 204
7.3.2 整形 206
7.4 旋压和强力旋压 206
7.4.1 旋压 206
7.4.2 强力旋压(亦称旋薄) 207
第8章 镁合金冲压板材的技术特点 212
8.1 镁合金板材的冲压成形性能 212
8.1.1 镁合金板材的拉伸试验及性能指标 212
8.1.2 镁合金的杯突试验 214
8.1.3 镁合金的扩孔试验 215
8.1.4 镁合金的拉深试验 216
8.1.5 镁合金的弯曲实验 216
8.2 镁合金板材的成形极限曲线 220
8.2.1 镁合金板材的成形极限试验原理和方法 220
8.2.2 镁合金试验结果 222
8.2.3 影响镁合金板材成型极限图的因素 223
8.2.4 FLD曲线在MAZ31镁合金板材冷成型中的应用 224
8.3 镁合金冲压技术 226
8.3.1 冲压模具的设计和制造 226
8.3.2 冲压工艺参数的选择 226
8.4 手机外壳和笔记本电脑外壳的冲压工艺 229
第9章 镁合金挤压工艺 233
9.1 概论 233
9.1.1 挤压基本类型 233
9.1.2 镁合金挤压技术的特点 234
9.1.3 镁合金的挤压工艺 234
9.2 挤压的基本原理 240
9.2.1 挤压的变形过程 240
9.2.2 挤压变形时的应力与应变 241
9.2.3 挤压变形时金属的流动 242
9.2.4 镁合金挤压制品的组织与性能 244
9.3 挤压变形力的计算 252
9.3.1 挤压力的确定 252
9.3.2 影响单位挤压力的主要因素 253
9.3.3 黑色金属挤压变形力的计算 260
9.3.4 有色金属及镁合金挤压力的计算 266
9.4 挤压设备的选择 268
9.4.1 冷挤压变形力-行程曲线分析 268
9.4.2 挤压工艺对设备的要求 269
9.4.3 挤压设备的选用 271
9.4.4 主要挤压机介绍 274
9.5 挤压工艺设计 276
9.5.1 挤压件图的设计 276
9.5.2 毛坯尺寸的计算 282
9.5.3 许用变形程度 284
9.6 镁合金挤压实例 289
9.6.1 镁合金散热片挤压成形工艺 289
9.6.2 其他镁合金挤压管材及型材的开发 290
第10章 挤压模具 292
10.1 挤压模具结构分析 292
10.1.1 挤压工艺对模具的要求 292
10.1.2 挤压模具与冲模比较 292
10.1.3 挤压模具分类 292
10.1.4 挤压模具零件的分类 295
10.2 挤压模具工作零件设计 296
10.2.1 正挤压模具工作零件设计 296
10.2.2 反挤压模具工作零件设计 300
10.2.3 组合凹模设计 307
10.2.4 卸件和顶出装置的设计 313
10.2.5 承压垫板的设计 315
10.2.6 模具导向装置的设计 316
10.3 镁合金挤压模具的特点 317
- 《材料成形技术基础》周志明,涂坚,盛旭敏主编 2019
- 《塑料成型工艺与模具设计》王春艳 2018
- 《塑料模具CAE技术及应用》陈开源主编 2019
- 《高分子材料成形工艺学》应宗荣编著 2019
- 《先进注塑模具图解》(德)哈里·布鲁纳(Harry Pruner),(德)沃尔夫冈·那什(Wolfgang Nesch)著 2019
- 《基于形状记忆合金的自复位抗震钢结构:材料、构件与体系》王伟 2020
- 《冲压成形原理与方法=PRINCIPLE AND METHOD OF STAMPING FORMING》于洋 2020
- 《金属空心构件先进冷成形技术》郭训忠,徐勇,陶杰著 2019
- 《不同磁性合金的磁场干摩擦机理及特性》魏永辉 2019
- 《模具数控加工技术》范鹤,曲树德主编 2019
- 《市政工程基础》杨岚编著 2009
- 《家畜百宝 猪、牛、羊、鸡的综合利用》山西省商业厅组织技术处编著 1959
- 《《道德经》200句》崇贤书院编著 2018
- 《高级英语阅读与听说教程》刘秀梅编著 2019
- 《计算机网络与通信基础》谢雨飞,田启川编著 2019
- 《看图自学吉他弹唱教程》陈飞编著 2019
- 《法语词汇认知联想记忆法》刘莲编著 2020
- 《培智学校义务教育实验教科书教师教学用书 生活适应 二年级 上》人民教育出版社,课程教材研究所,特殊教育课程教材研究中心编著 2019
- 《国家社科基金项目申报规范 技巧与案例 第3版 2020》文传浩,夏宇编著 2019
- 《流体力学》张扬军,彭杰,诸葛伟林编著 2019
- 《中国当代乡土小说文库 本乡本土》(中国)刘玉堂 2019
- 《异质性条件下技术创新最优市场结构研究 以中国高技术产业为例》千慧雄 2019
- 《中国铁路人 第三届现实主义网络文学征文大赛一等奖》恒传录著 2019
- 《莼江曲谱 2 中国昆曲博物馆藏稀见昆剧手抄曲谱汇编之一》郭腊梅主编;孙伊婷副主编;孙文明,孙伊婷编委;中国昆曲博物馆编 2018
- 《中国制造业绿色供应链发展研究报告》中国电子信息产业发展研究院 2019
- 《中国陈设艺术史》赵囡囡著 2019
- 《指向核心素养 北京十一学校名师教学设计 英语 七年级 上 配人教版》周志英总主编 2019
- 《《走近科学》精选丛书 中国UFO悬案调查》郭之文 2019
- 《清至民国中国西北戏剧经典唱段汇辑 第8卷》孔令纪 2018
- 《北京生态环境保护》《北京环境保护丛书》编委会编著 2018