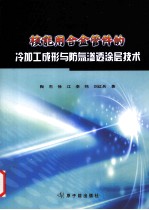
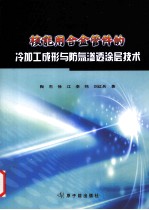
核能用合金管件的冷加工成形与防氚渗透涂层技术PDF电子书下载
- 电子书积分:11 积分如何计算积分?
- 作 者:陶杰等著
- 出 版 社:北京:原子能出版社
- 出版年份:2009
- ISBN:9787502247041
- 页数:259 页
第1章 核电用管件发展概况 1
1.1 世界核电的发展 1
1.2 核电在我国的发展 2
1.2.1 我国发展核电的基本方针 4
1.2.2 中国核电建设进入批量建设阶段 4
1.3 核能的未来发展 5
1.3.1 第三代反应堆 6
1.3.2 第四代反应堆 7
1.3.3 聚变堆 13
1.4 核能应用对金属管道与管件的要求 14
1.4.1 裂变堆材料 14
1.4.2 聚变堆材料 15
第2章 管件冷成形原理 18
2.1 金属塑性成形基础 18
2.2 管材弯曲加工 19
2.2.1 管材弯曲成形工艺分类 19
2.2.2 弯曲加工原理 21
2.2.3 弯管成形过程 24
2.2.4 影响管材弯曲成形的主要因素 24
2.2.5 管材弯曲主要参数计算设计 25
2.2.6 管材弯曲成形工艺研究现状 29
2.3 管材胀形加工 31
2.3.1 胀形方法分类 31
2.3.2 液压胀形三通管件的特点 33
2.3.3 胀形加工原理(自由胀形、轴向压缩胀形、复合胀形) 34
2.3.4 管材胀形成形过程 38
2.3.5 影响管材胀形成形的主要因素 39
2.3.6 胀形工艺的研究进展 41
第3章 管件冷成形数值模拟 45
3.1 有限元数值模拟技术 45
3.1.1 有限元数值模拟技术的提出和发展 45
3.1.2 塑性有限元的基本概念 46
3.1.3 弹塑性有限元和刚塑性有限元的基本理论 46
3.1.4 有限元的一般解题步骤 47
3.1.5 有限元软件简介 52
3.2 弯管冷成形数值模拟 54
3.2.1 弯管有限元模型 54
3.2.2 模具参数对弯管成形质量的影响 56
3.2.3 工艺参数对成形质量的影响 58
3.2.4 小结 61
3.3 三通管冷成形数值模拟 62
3.3.1 三通管有限元模型 62
3.3.2 成形力对三通管成形质量的影响 65
3.3.3 工艺参数对成形质量的影响 71
3.3.4 小结 72
第4章 核电用不锈钢管件冷成形加工 75
4.1 核电用不锈钢管坯铸/锻加工 75
4.2 冷轧加工 76
4.2.1 冷轧工艺原理 77
4.2.2 冷轧工艺实施 77
4.2.3 冷轧工艺关键控制技术 78
4.3 核电用不锈钢薄壁管件的冷成形 78
4.3.1 薄壁不锈钢三通管件的成形技术 79
4.3.2 不锈钢异径接头的成形 80
4.4 核能用不锈钢为基材的复合管件成形工艺 81
4.4.1 试验装置及工艺原理 82
4.4.2 有限元模型 82
4.4.3 有限元模拟结果 83
4.4.4 316L/Al复合管实际成形 86
4.5 核电用不锈钢管件的其他加工工艺 87
4.5.1 超大型三通加工方法 87
4.5.2 弯管的无模成形方法 88
4.5.3 弯管的激光成形方法 89
4.5.4 矩形方管的变曲率推弯方法 89
4.6 核电管件冷成形残余应力及热处理 90
4.7 核电用不锈钢管件酸洗处理 90
4.7.1 不锈钢氧化皮的特性 90
4.7.2 清除核电不锈钢表面氧化皮的方法 91
4.7.3 酸洗钝化方法及有害元素的控制 91
4.8 核电用不锈钢管件质量控制手段与措施 92
4.8.1 核电用不锈钢管材制备的控制与检测 92
4.8.2 核电用不锈钢管件质量检测 92
4.9 本章小结与展望 94
第5章 低活性马氏体钢管件冷成形技术 98
5.1 低活性马氏体钢的研究进展 98
5.1.1 国际研究综述 98
5.1.2 国内研究综述 99
5.2 CLAM钢的力学性能特点 100
5.2.1 成分特点 100
5.2.2 组织结构与热处理工艺 100
5.2.3 机械性能 101
5.2.4 变形加工性能特点 103
5.3 CLAM钢管件的冷成形加工关键技术与数值模拟 103
5.3.1 冷成形加工关键技术 104
5.3.2 数值模拟 105
5.3.3 弯头冷成形数值模拟 105
5.3.4 正三通冷成形数值模拟 110
5.3.5 斜三通冷成形数值模拟 117
5.4 CLAM钢管件冷成形加工过程的组织变化与尺寸控制 123
5.4.1 冷成形加工过程的组织变化分析 123
5.4.2 弯头的尺寸控制技术 123
5.4.3 三通的尺寸控制技术 124
5.5 CLAM钢管件的实际冷加工工艺 125
5.5.1 弯头冷成形工艺 125
5.5.2 正/斜三通冷成形工艺 125
5.5.3 CLAM钢管件质量控制与检验 126
5.6 本章小结与展望 127
5.6.1 小结 127
5.6.2 研究展望 128
第6章 防氚及氢同位素渗透玻璃质壁垒层的制备技术 130
6.1 玻璃质壁垒层在防氚及氢同位素渗透技术中的应用及意义 130
6.1.1 现有壁垒层存在的问题 131
6.1.2 玻璃质陶瓷涂层 131
6.1.3 玻璃质陶瓷涂层的主要应用领域 132
6.1.4 玻璃质陶瓷涂层在阻止氢和氢同位素渗透领域的新应用 132
6.2 防氚及氢同位素渗透玻璃质壁垒层用玻璃熔块成分设计 133
6.2.1 设计原则 133
6.2.2 涂层成分设计的方法 134
6.3 防氚及氢同位素渗透玻璃质壁垒层的制备 137
6.3.1 原材料的选择 137
6.3.2 防氚及氢同位素渗透玻璃质壁垒层的制备工艺 137
6.4 影响防氚及氢同位素渗透玻璃质壁垒层制备质量的因素及改善方法 140
6.4.1 水溶性高分子化合物M及釉浆pH值对玻璃质壁垒层制备质量的影响 140
6.4.2 涂层与基体的润湿性对玻璃质壁垒层制备质量的影响 143
6.5 玻璃质壁垒层作为防氚及氢同位素渗透壁垒层的实际应用及性能评价 147
6.5.1 涂层的显微分析 147
6.5.2 涂层与基体的结合性能试验与分析 151
6.5.3 涂层阻氢性能评价及其阻氢机制探讨 153
6.5.4 搪瓷壁垒层阻氢机理的探讨 159
6.6 本章小结与展望 160
6.6.1 小结 160
6.6.2 玻璃质陶瓷壁垒层研究展望 161
第7章 双辉等离子表面冶金技术 165
7.1 双辉技术的形成 165
7.2 双辉等离子表面冶金技术原理 165
7.2.1 双辉的物理基础 166
7.2.2 双层辉光离子渗金属技术优缺点 169
7.3 双辉等离子渗金属技术的研究进展 170
7.3.1 单元渗 170
7.3.2 两元渗 177
7.3.3 双辉多元共渗技术 179
7.3.4 复合镀渗层 185
7.3.5 复合镀渗层耐蚀性能 190
7.4 双辉等离子金属—非金属共渗技术研究现状 190
7.4.1 Ti-N共渗工艺研究 190
7.4.2 氮化钛渗镀复合层的组织结构 193
7.5 基于双阴极放电低温沉积技术研究的初探 195
7.5.1 Al-Mg合金层 195
7.5.2 Al-Cr-Fe表面合金层 198
7.5.3 镁合金表面形成Ni-Cr-Mo-Cu合金层 202
第8章 双层辉光等离子渗技术制备Al2O3防氚渗透涂层 208
8.1 氧化铝涂层概述 208
8.2 试验设备、材料及方法 208
8.2.1 试验设备 208
8.2.2 试验材料 209
8.2.3 涂层制备方法 209
8.3 316L不锈钢表面渗铝层的制备及性能表征 210
8.3.1 渗铝层的制备 210
8.3.2 渗铝层显微观察及能谱分析 210
8.3.3 渗铝层与316L不锈钢基体的界面结合 211
8.3.4 渗铝层相结构分析 212
8.3.5 工艺参数对渗铝层的影响 213
8.4 316L不锈钢表面Al2O3涂层的制备及表征 214
8.4.1 显微组织 214
8.4.2 Al2O3涂层与基体界面的结合 217
8.4.3 Al2O3涂层相结构分析 217
8.4.4 氧化机理分析与讨论 220
8.5 Al2O3涂层性能表征 222
8.5.1 划痕试验 222
8.5.2 抗热震性能测试 225
8.5.3 耐腐蚀性能表征 226
8.5.4 摩擦学性能表征 227
8.6 本章小结 229
第9章 双层辉光等离子渗技术制备Cr2O3防氚渗透涂层 233
9.1 概述 233
9.1.1 Cr2O3涂层简介 233
9.1.2 渗铬、渗氧技术概述 233
9.2 双层辉光离子渗铬及渗氧工艺设计 234
9.2.1 实验材料及设备 234
9.2.2 工艺参数的选择 234
9.3 渗铬层组织结构与结合性能研究 234
9.3.1 渗铬层的形貌 235
9.3.2 渗铬层的铬浓度分布 235
9.3.3 渗铬层的物相分析 237
9.4 Cr2O3涂层的制备及表征 237
9.4.1 Cr2O3涂层的形貌 238
9.4.2 Cr2O3涂层的铬氧浓度分布 241
9.4.3 Cr2O3涂层的物相分析 242
9.4.4 Cr2O3涂层表面微观结构分析 243
9.4.5 双层辉光离子渗氧机理研究 243
9.5 Cr2O3涂层的性能研究 244
9.5.1 不同氧流量下Cr2O3涂层的电化学腐蚀性能研究 244
9.5.2 不同氧流量下Cr2O3涂层的抗热震性能研究 246
9.5.3 不同氧流量下Cr2O3涂层的划痕性能研究 247
9.5.4 不同氧流量下Cr2O3涂层的摩擦磨损性能研究 247
9.6 本章小结 249
第10章 防氚渗透涂层阻氚机理研究 253
10.1 氚同位素分子的扩散渗透模型 253
10.1.1 氚同位素分子在金属中的扩散渗透模型 253
10.1.2 氚同位素分子在防氚渗透涂层中的扩散渗透模型 253
10.1.3 防氚渗透涂层的阻氚机理模型 254
10.2 防氚渗透涂层的阻氚机理 254
10.2.1 不同材料体系防氚渗透涂层的阻氚机理 254
10.2.2 不同表面结构涂层的阻氚机理 255
10.2.3 不同表面质量涂层的阻氚机理 256
10.2.4 具有不同表面吸附系数和解析系数涂层的阻氚机理 257
10.2.5 复合涂层的阻氚机理 257
10.3 总结和展望 258
- 《激光加工实训技能指导理实一体化教程 下》王秀军,徐永红主编;刘波,刘克生副主编 2017
- 《先进激光加工技能实训》肖海兵主编 2019
- 《菜籽油加工技术》罗质主编 2019
- 《材料成形技术基础》周志明,涂坚,盛旭敏主编 2019
- 《蔬菜腌制加工技术》闫广金著 2019
- 《高分子材料与加工实验教程》刘昕责任编辑;(中国)胡扬剑,舒友,罗琼林 2019
- 《中药材加工、鉴质实用技术》周至杰 2019
- 《高分子材料成形工艺学》应宗荣编著 2019
- 《脉冲电场食品非热加工技术》曾新安主编 2019
- 《刺五加生产加工适宜技术》李晓琳,张顺捷主编 2018
- 《指向核心素养 北京十一学校名师教学设计 英语 七年级 上 配人教版》周志英总主编 2019
- 《北京生态环境保护》《北京环境保护丛书》编委会编著 2018
- 《指向核心素养 北京十一学校名师教学设计 英语 九年级 上 配人教版》周志英总主编 2019
- 《高等院校旅游专业系列教材 旅游企业岗位培训系列教材 新编北京导游英语》杨昆,鄢莉,谭明华 2019
- 《中国十大出版家》王震,贺越明著 1991
- 《近代民营出版机构的英语函授教育 以“商务、中华、开明”函授学校为个案 1915年-1946年版》丁伟 2017
- 《指向核心素养 北京十一学校名师教学设计 数学 九年级 上 配人教版》周志英总主编 2019
- 《西单大杂院-北京老舍文学院首届中青年作家高研班学员小说作品集》北京老舍文学院编 2019
- 《指向核心素养 北京十一学校名师教学设计 数学 七年级 上 配人教版》周志英总主编 2019
- 《国之重器出版工程 云化虚拟现实技术与应用》熊华平 2019