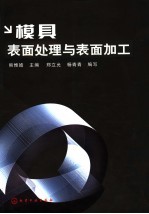
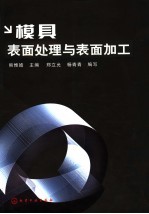
模具表面处理与表面加工PDF电子书下载
- 电子书积分:16 积分如何计算积分?
- 作 者:熊惟皓主编
- 出 版 社:北京:化学工业出版社
- 出版年份:2007
- ISBN:7502590145
- 页数:526 页
上篇 模具表面处理 3
第1章 模具的服役条件、失效形式及失效分析 3
1.1 模具的服役条件及失效形式 3
1.1.1 冷作模具的服役条件及失效形式 3
1.1.2 热作模具的服役条件及失效形式 6
1.1.3 塑料模具的服役条件及失效形式 9
1.2 模具失效分析 9
1.2.1 模具失效 9
1.2.2 影响模具失效的主要因素 10
1.2.3 模具失效分析方法 14
1.2.4 模具失效分析实例 15
参考文献 21
第2章 模具的表面处理方法 22
2.1 模具的服役条件对表面处理的要求 22
2.1.1 冷作模具的服役条件对表面处理的要求 22
2.1.2 热作模具的服役条件对表面处理的要求 23
2.1.3 塑料模具的服役条件对表面处理的要求 24
2.2 模具表面处理方式概述 25
2.2.1 模具表面处理的分类与特点 25
2.2.2 表面强化处理在模具中的应用 27
2.2.3 模具表面强化处理时应注意的问题 29
2.2.4 模具常用表面处理方法简介 31
参考文献 33
第3章 表面化学热处理 34
3.1 概述 34
3.2 渗碳 35
3.2.1 渗碳的基本原理 35
3.2.2 影响渗碳质量的主要因素 36
3.2.3 渗碳工艺 37
3.2.4 渗碳层的检验及组织缺陷分析 45
3.2.5 渗碳实例 46
3.3 渗氮 47
3.3.1 渗氮的基本原理 48
3.3.2 渗氮工艺 50
3.3.3 渗氮层的检验及组织缺陷分析 55
3.3.4 渗氮实例 57
3.4 渗硼 59
3.4.1 渗硼层组织与性能 59
3.4.2 影响渗硼层质量的主要因素 61
3.4.3 渗硼工艺 62
3.4.4 渗硼层的检验及组织缺陷 66
3.4.5 渗硼实例 67
3.5 渗金属 68
3.5.1 渗金属的基本原理 69
3.5.2 固体粉末渗铬 72
3.5.3 硼砂盐浴渗钛 75
3.5.4 硼砂盐浴渗铌 76
3.5.5 渗钒 77
3.5.6 真空渗金属 79
3.5.7 离子渗金属 79
3.5.8 渗金属实例 81
3.6 多元共渗 82
3.6.1 硼砂盐浴铬钒共渗工艺 82
3.6.2 铬铝共渗工艺 83
3.6.3 硼钒共渗工艺 84
3.6.4 多元共渗应用实例 86
参考文献 88
第4章 气相沉积技术 89
4.1 概述 89
4.1.1 气相沉积技术及其分类 89
4.1.2 气相沉积技术的应用 89
4.2 物理气相沉积 90
4.2.1 物理气相沉积概述 90
4.2.2 真空蒸镀 92
4.2.3 溅射镀膜 97
4.2.4 离子镀膜 102
4.2.5 物理气相沉积实例 110
4.3.1 化学气相沉积的原理 111
4.3 化学气相沉积 111
4.3.2 化学气相沉积的设备及工艺过程 113
4.3.3 化学气相沉积层的组织结构及影响镀层质量的因素 114
4.3.4 化学气相沉积的特点及分类 116
4.3.5 等离子体化学气相沉积 117
4.3.6 激光化学气相沉积 119
4.3.7 金属有机化合物化学气相沉积和低压化学气相沉积 121
4.3.8 化学气相沉积实例 121
参考文献 124
5.1.2 电镀的基本原理 126
5.1.1 概述 126
5.1 电镀 126
第5章 电镀与化学镀 126
5.1.3 电镀铬 127
5.1.4 电镀镍 135
5.1.5 模具表面电镀实例 138
5.2 电刷镀 140
5.2.1 电刷镀的基本原理 140
5.2.2 电刷镀的设备 141
5.2.3 镀液的配制 143
5.2.4 电刷镀的表面准备及温度控制 147
5.2.5 电刷镀工艺及特点 148
5.2.6 镀镍层缺陷的形成原因及预防 151
5.2.7 电刷镀应用实例 152
5.3 复合电刷镀 153
5.3.1 复合电刷镀的基本原理 154
5.3.2 复合镀液的制备 155
5.3.3 复合电刷镀的工艺特点 159
5.3.4 复合镀层的性能 160
5.3.5 复合电刷镀的应用 163
5.4 化学镀镍磷合金 164
5.4.1 化学镀的基本原理 164
5.4.2 化学镀镍磷溶液的配制及影响因素 165
5.4.3 化学镀镍磷的组织结构 167
5.4.4 化学镀应用实例 168
参考文献 171
第6章 热喷涂技术 172
6.1 概述 172
6.1.1 热喷涂的一般原理 172
6.1.2 热喷涂发展历史概况 173
6.1.3 热喷涂方法分类与技术特点 174
6.1.4 热喷涂材料分类及生产方法 174
6.1.5 热喷涂材料的选择 176
6.2 火焰喷涂 179
6.2.1 线材火焰喷涂 179
6.2.3 高速火焰粉末喷涂 181
6.2.2 火焰粉末喷涂 181
6.2.4 火焰喷涂的应用 184
6.3 电弧喷涂 184
6.3.1 电弧喷涂的原理及特点 184
6.3.2 电弧喷涂设备 185
6.3.3 电弧喷涂材料及其选择 185
6.4 等离子喷涂 186
6.4.1 等离子喷涂的基本原理及特点 186
6.4.2 等离子喷涂工艺 187
6.4.3 低压等离子喷涂 187
6.4.4 超音速等离子喷涂 189
6.4.5 粉末等离子喷焊(堆焊) 191
6.4.6 等离子喷涂应用实例 192
6.5 火焰粉末喷熔及重熔 193
6.5.1 火焰粉末喷熔及重熔的基本原理与特点 193
6.5.2 火焰粉末喷熔及重熔工艺 195
6.5.3 火焰粉末喷熔及重熔技术的应用 197
参考文献 197
第7章 激光表面处理 198
7.1 概述 198
7.1.1 激光和激光器 198
7.1.2 激光加热的特点及用途 201
7.2.1 激光相变硬化的原理 204
7.2 激光表面相变硬化 204
7.2.2 激光相变硬化工艺及特点 205
7.2.3 激光相变硬化对模具表面特性的影响 207
7.2.4 激光相变硬化应用实例 208
7.3 激光熔凝、激光非晶化及激光冲击硬化 209
7.3.1 激光熔凝 209
7.3.2 激光非晶化 210
7.4 激光表面熔覆 212
7.4.1 激光表面熔覆的原理及特点 212
7.3.3 激光冲击硬化 212
7.4.2 激光表面熔覆工艺及特点 213
7.4.3 激光表面熔覆材料 214
7.4.4 激光表面熔覆应用实例 215
7.5 激光表面合金化 216
7.5.1 激光表面合金化的原理与特性 216
7.5.2 激光表面合金化工艺与设备 217
7.5.3 激光表面合金化的工业应用前景 221
7.6 其他激光表面处理技术 221
参考文献 222
8.1.1 离子注入的发展过程 224
8.1.2 离子注入表面改性的特点 224
8.1 概述 224
第8章 离子注入技术 224
8.1.3 离子注入原理及方式 225
8.1.4 离子注入对金属材料的改性作用 226
8.2 离子注入设备 228
8.2.1 离子注入设备的组成 228
8.2.2 离子注入机的分类 228
8.2.3 离子注入机各组成部分简介 230
8.3 离子注入的表面强化机制 238
8.3.1 离子注入物理过程 238
8.3.2 强化作用机制及影响因素 239
8.4.1 离子注入工艺 241
8.4 离子注入工艺及注入层的特性 241
8.4.2 注入层的成分、相结构和性能 242
8.4.3 离子注入技术的发展 244
8.5 离子注入应用实例 245
参考文献 247
第9章 电子束强化技术 248
9.1 概述 248
9.1.1 电子束强化技术 248
9.1.2 电子束的性质 248
9.1.3 电子束与固体的作用 249
9.2 电子束表面相变硬化 251
9.2.1 电子束加热相变原理及其工艺 251
9.2.2 金属材料的电子束相变硬化 256
9.2.3 电子束加热与激光束加热的比较 259
9.3.1 电子束表面合金化原理及其工艺 261
9.3 电子束表面合金化 261
9.3.2 金属材料的电子束合金化处理 263
9.4 电子束熔凝处理 265
9.4.1 电子束熔凝处理原理及其工艺 265
9.4.2 金属材料的电子束熔凝处理 268
9.5 电子束强化应用实例 270
参考文献 271
10.1 镀渗工艺 272
10.1.1 概述 272
第10章 其他表面处理技术 272
10.1.2 高速钢冷作模具镀渗Co-W-Ti三元合金镀渗层 273
10.1.3 模具化学镀Ni-P合金和渗硼的镀渗处理 274
10.2 TD处理工艺 276
10.2.1 TD处理的工艺及特点 276
10.2.2 涂层的质量控制 278
10.2.3 涂层的各项性能 279
10.2.4 TD处理应用实例 280
10.3 电火花表面处理 281
10.3.1 电火花表面处理的基本原理和特点 281
10.3.2 强化层的特性 284
10.3.3 模具电火花强化工艺 286
10.3.4 电火花表面处理应用实例 290
10.4 火焰表面淬火 292
10.4.1 火焰表面淬火的特点 292
10.4.2 火焰表面淬火的工艺及方法 293
10.4.3 火焰表面淬火用模具材料 294
10.4.4 火焰表面淬火应用实例 294
参考文献 296
下篇 模具表面加工 299
第11章 电火花加工 299
11.1 电火花加工的基本原理、特点与分类 299
11.1.1 电火花加工的基本原理 299
11.1.2 电火花加工的特点 303
11.1.3 电火花加工的分类 304
11.2 电火花穿孔成形加工 305
11.2.1 电火花穿孔成形加工机床的结构与分类 305
11.2.2 电火花穿孔成形加工中的基本规律 317
11.2.3 电火花穿孔成形加工方法 325
11.2.4 工具电极 329
11.2.5 工件的准备 336
11.2.6 工具电极和工件的装夹与校正定位 336
11.2.7 电规准的选择和转换 339
11.2.8 数控电火花穿孔成形加工的手工编程 340
11.2.9 电火花穿孔成形加工在模具加工中的应用实例 342
11.3.1 电火花线切割加工的原理 345
11.3 数控电火花线切割加工 345
11.3.2 电火花线切割加工的特点 346
11.3.3 数控电火花线切割加工机床 347
11.3.4 电火花线切割加工中的基本规律 353
11.3.5 工件的装夹和找正 358
11.3.6 电极丝位置的调整和垂直度的校正 360
11.3.7 电规准的选择 361
11.3.8 变频进给速度的调整 362
11.3.9 数控电火花线切割加工编程 363
参考文献 370
12.1 电解加工 372
第12章 电化学加工 372
12.1.1 电解加工的原理 373
12.1.2 电解加工的特点 374
12.1.3 电解加工的设备 375
12.1.4 电解液 379
12.1.5 电解加工中的基本规律 384
12.1.6 电解加工在模具加工中的应用实例 395
12.2 电解磨削 396
12.2.1 电解磨削的原理 396
12.2.2 电解磨削的特点 398
12.2.3 电解磨削设备 398
12.2.4 电解液 399
12.2.5 电解磨轮 400
12.2.6 电解磨削中的基本规律 402
12.2.7 电解磨削方式 404
12.2.8 电解磨削工艺 404
12.3 电铸 408
12.3.1 电铸的原理 409
12.3.2 电铸的特点 409
12.3.3 电铸设备 410
12.3.4 电铸的工艺流程 410
12.3.5 电铸工艺在模具加工中的应用实例 413
参考文献 414
13.1.1 快速成形的原理 415
第13章 快速成形与快速模具制造 415
13.1 快速成形 415
13.1.2 快速成形的特点 416
13.1.3 快速成形的工艺流程 416
13.1.4 快速成形的材料 419
13.1.5 典型快速成形工艺 419
13.2 快速模具制造 432
13.2.1 直接快速模具制造 433
13.2.2 间接快速模具制造 434
参考文献 442
14.1.1 仿形雕刻 443
第14章 图形刻蚀加工 443
14.1 机械雕刻 443
14.1.2 数控雕刻 445
14.2 化学刻蚀 446
14.2.1 化学刻蚀的原理 446
14.2.2 化学刻蚀的特点 447
14.2.3 化学刻蚀的工艺流程 447
14.3 照相腐蚀 449
14.3.1 照相腐蚀的原理 449
14.3.2 照相腐蚀的特点 449
14.3.3 照相腐蚀的工艺流程 449
14.4.1 电火花成形电极雕刻 455
14.4 电火花雕刻 455
14.4.2 计算机辅助电火花雕刻(电火花展成法雕刻) 456
14.4.3 电火花刻字 457
14.5 激光雕刻 458
14.5.1 激光雕刻的原理 458
14.5.2 激光雕刻的特点 458
14.5.3 激光雕刻机 459
参考文献 459
第15章 光整加工 460
15.1 研磨 460
15.1.2 研磨的特点 461
15.1.1 研磨的原理 461
15.1.3 研磨的方法 462
15.1.4 研磨剂 462
15.1.5 研具 465
15.1.6 自动研抛装置 468
15.1.7 研磨效率和研磨质量的影响因素 471
15.1.8 手工研磨工艺 474
15.1.9 超精密研磨 475
15.1.10 浮动研磨 475
15.1.11 弹性发射加工 476
15.2.2 抛光工具 478
15.2.3 抛光质量的影响因素 478
15.2.1 抛光的原理 478
15.2 抛光 478
15.2.4 抛光工艺 479
15.2.5 弹性体蠕动抛光 480
15.2.6 可挠曲片状油石抛光 481
15.2.7 液体磨料与铁粉刷抛光 481
15.3 超精研抛 481
15.3.1 超精研抛的原理 481
15.3.2 超精研抛的特点 484
15.3.3 超精研抛具 484
15.3.5 超精研抛的工艺参数 486
15.3.4 超精研抛液 486
15.4 电解抛光 487
15.4.1 电解抛光的原理 488
15.4.2 电解抛光的特点 489
15.4.3 电解抛光质量的影响因素 489
15.4.4 电解抛光的工艺流程 491
15.5 化学抛光 492
15.5.1 化学抛光的原理 492
15.5.2 化学抛光的特点 493
15.5.3 化学抛光质量和效率的影响因素 493
15.6.2 电解修磨抛光的特点 494
15.6 电解修磨抛光 494
15.6.1 电解修磨抛光的原理 494
15.6.3 电解修磨抛光装置 495
15.6.4 电解修磨抛光质量和效率的影响因素 497
15.6.5 电解修磨抛光工艺 497
15.7 磁力研抛 498
15.7.1 磁力研抛的原理 498
15.7.2 磁力研抛的特点 499
15.7.3 磁力研抛装置和磁性磨料 499
15.7.4 磁力研抛质量和效率的影响因素 500
15.8 超声波抛光 502
15.7.5 磁力研抛在模具加工中的应用实例 502
15.8.1 超声波的特性 503
15.8.2 超声波抛光的原理 503
15.8.3 超声波抛光的特点 504
15.8.4 超声波抛光设备 504
15.8.5 超声波抛光中的基本规律 509
15.8.6 超声波抛光在模具加工中的应用实例 512
15.8.7 超声波电解复合抛光 512
15.8.8 超声波电火花复合抛光 514
15.9.1 挤压珩磨的原理 516
15.9.2 挤压珩磨的特点 516
15.9 挤压珩磨 516
15.9.3 挤压珩磨装置 517
15.9.4 挤压珩磨工艺参数的选择 519
15.9.5 挤压珩磨在模具加工中的应用实例 519
15.10 玻璃珠喷射加工 520
15.10.1 玻璃珠喷射加工的原理 520
15.10.2 玻璃珠喷射加工的特点 521
15.10.3 玻璃珠喷射加工装置 521
15.10.4 玻璃珠喷射加工质量和效率的影响因素 521
参考文献 522
附录一 准备功能G代码(JB 3082—83) 525
附录二 辅助功能M代码(JB 3082—83) 526
- 《大数据Hadoop 3.X分布式处理实战》吴章勇,杨强 2020
- 《烧结法处理非常规含铁资源研究》王哲著 2018
- 《无机元素原子光谱分析样品预处理技术》吴瑶庆 2019
- 《农村生活污水处理工艺与技术应用》李灵娜著 2019
- 《中国人民大学研究报告系列 中国水处理行业可持续发展战略研究报告 膜工业卷 3》(中国)郑祥,魏源送,王志伟 2019
- 《工业废水处理工艺与设计》高永编著 2019
- 《工业水处理技术》(中国)赵文玉,林华,许立巍 2019
- 《污水处理PPP项目实施方案编制实务》王雁然,方俊,朱立冬 2019
- 《塑料成型工艺与模具设计》王春艳 2018
- 《图像处理与图形界面(GUI)设计案例教程》李娜,张丽君 2019